CNC-Graviermaschinen beherrschen die Präzisionsbearbeitung mit kleinen Werkzeugen und verfügen über die Fähigkeit zum Fräsen, Schleifen, Bohren und Hochgeschwindigkeitsgewindeschneiden.Sie werden häufig in verschiedenen Bereichen wie der 3C-Industrie, der Formenindustrie und der Medizinindustrie eingesetzt.In diesem Artikel werden häufig gestellte Fragen zur CNC-Gravurbearbeitung gesammelt.
Was sind die Hauptunterschiede zwischen CNC-Gravur und CNC-Fräsen?
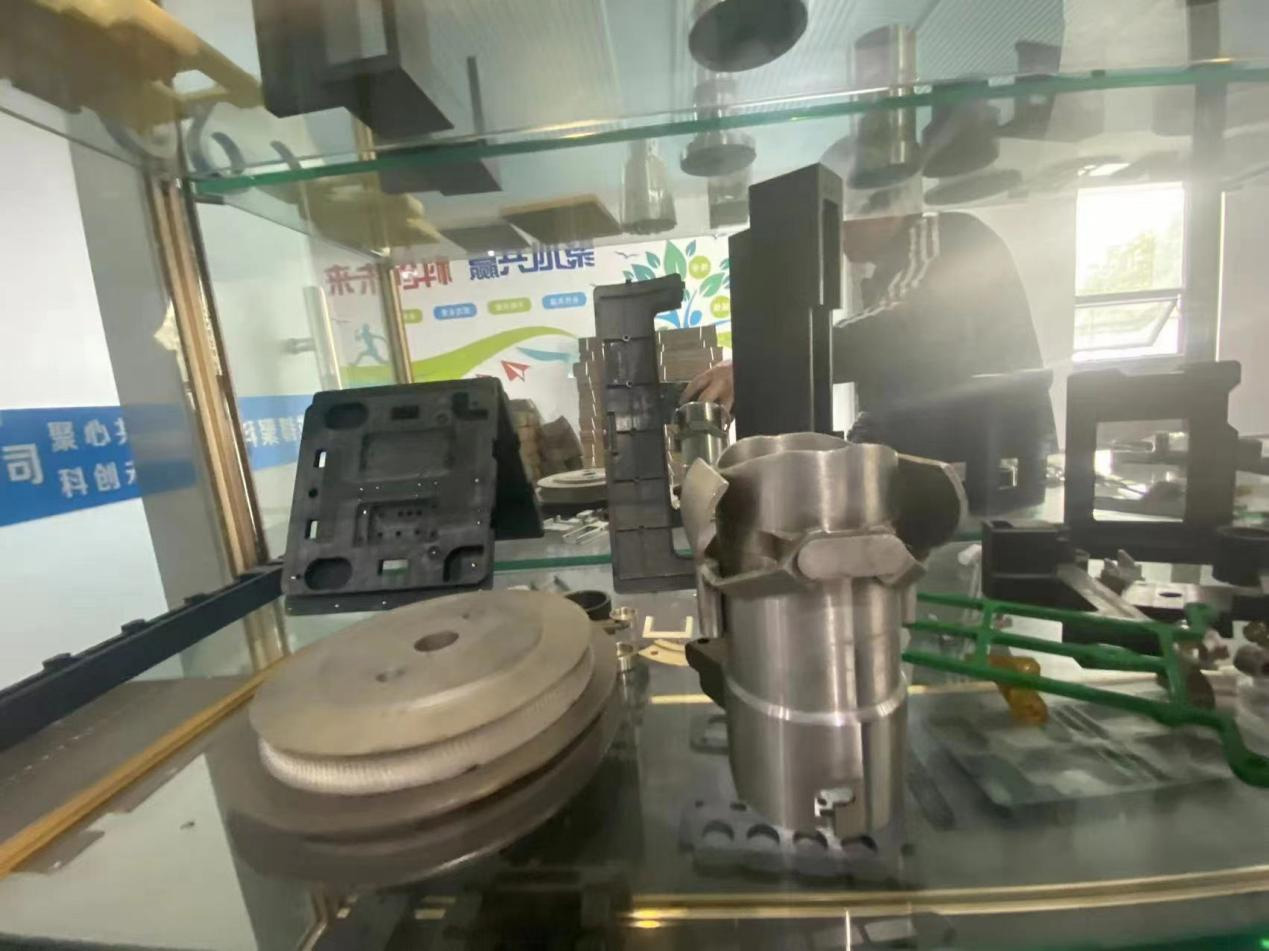
Sowohl CNC-Gravur- als auch CNC-Fräsverfahren nutzen Fräsprinzipien.Der Hauptunterschied liegt im verwendeten Werkzeugdurchmesser, wobei der üblicherweise verwendete Werkzeugdurchmesserbereich beim CNC-Fräsen zwischen 6 und 40 Millimeter liegt, während der Werkzeugdurchmesser bei der CNC-Gravurbearbeitung zwischen 0,2 und 3 Millimeter liegt.
Kann das CNC-Fräsen nur für die Grobbearbeitung verwendet werden, während die CNC-Gravur nur für die Präzisionsbearbeitung verwendet werden kann?
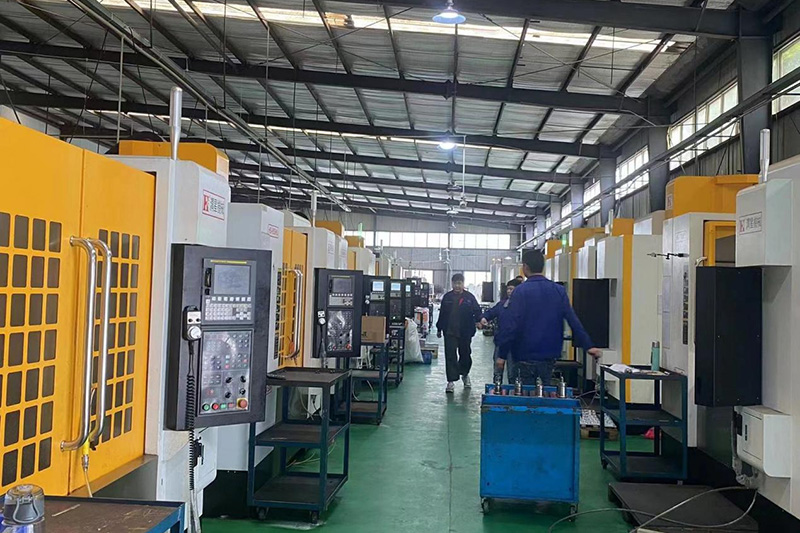
Bevor wir diese Frage beantworten, wollen wir zunächst das Konzept des Prozesses verstehen.Das Bearbeitungsvolumen der Grobbearbeitung ist groß, während das Bearbeitungsvolumen der Präzisionsbearbeitung klein ist, weshalb manche Menschen die Grobbearbeitung gewöhnlich als „schweres Schneiden“ und die Präzisionsbearbeitung als „leichtes Schneiden“ betrachten.Tatsächlich sind Grobbearbeitung, Halbpräzisionsbearbeitung und Präzisionsbearbeitung Prozesskonzepte, die unterschiedliche Bearbeitungsstufen darstellen.Die genaue Antwort auf diese Frage lautet also, dass beim CNC-Fräsen schwere oder leichte Schnitte möglich sind, während beim CNC-Gravieren nur leichte Schnitte möglich sind.
Kann das CNC-Gravierverfahren zur Grobbearbeitung von Stahlmaterialien eingesetzt werden?
Die Beurteilung, ob die CNC-Gravur ein bestimmtes Material verarbeiten kann, hängt hauptsächlich davon ab, wie groß das Werkzeug sein kann.Die bei der CNC-Gravurbearbeitung verwendeten Schneidwerkzeuge bestimmen die maximale Schneidkapazität.Wenn die Form der Form die Verwendung von Werkzeugen mit einem Durchmesser von mehr als 6 Millimetern zulässt, wird dringend empfohlen, zuerst das CNC-Fräsen zu verwenden und dann das restliche Material durch Schnitzen zu entfernen.
Kann das Hinzufügen eines Geschwindigkeitserhöhungskopfes zur Spindel des CNC-Bearbeitungszentrums die Gravurbearbeitung vervollständigen?
Nicht in der Lage zu vervollständigen.Dieses Produkt erschien vor zwei Jahren auf einer Ausstellung, der Schnitzprozess konnte jedoch nicht abgeschlossen werden.Der Hauptgrund liegt darin, dass die Konstruktion von CNC-Bearbeitungszentren ihren eigenen Werkzeugbereich berücksichtigt und die Gesamtstruktur nicht für die Gravurbearbeitung geeignet ist.Der Hauptgrund für diese falsche Vorstellung liegt darin, dass man die elektrische Hochgeschwindigkeitsspindel fälschlicherweise als einziges Merkmal der Graviermaschine betrachtete.
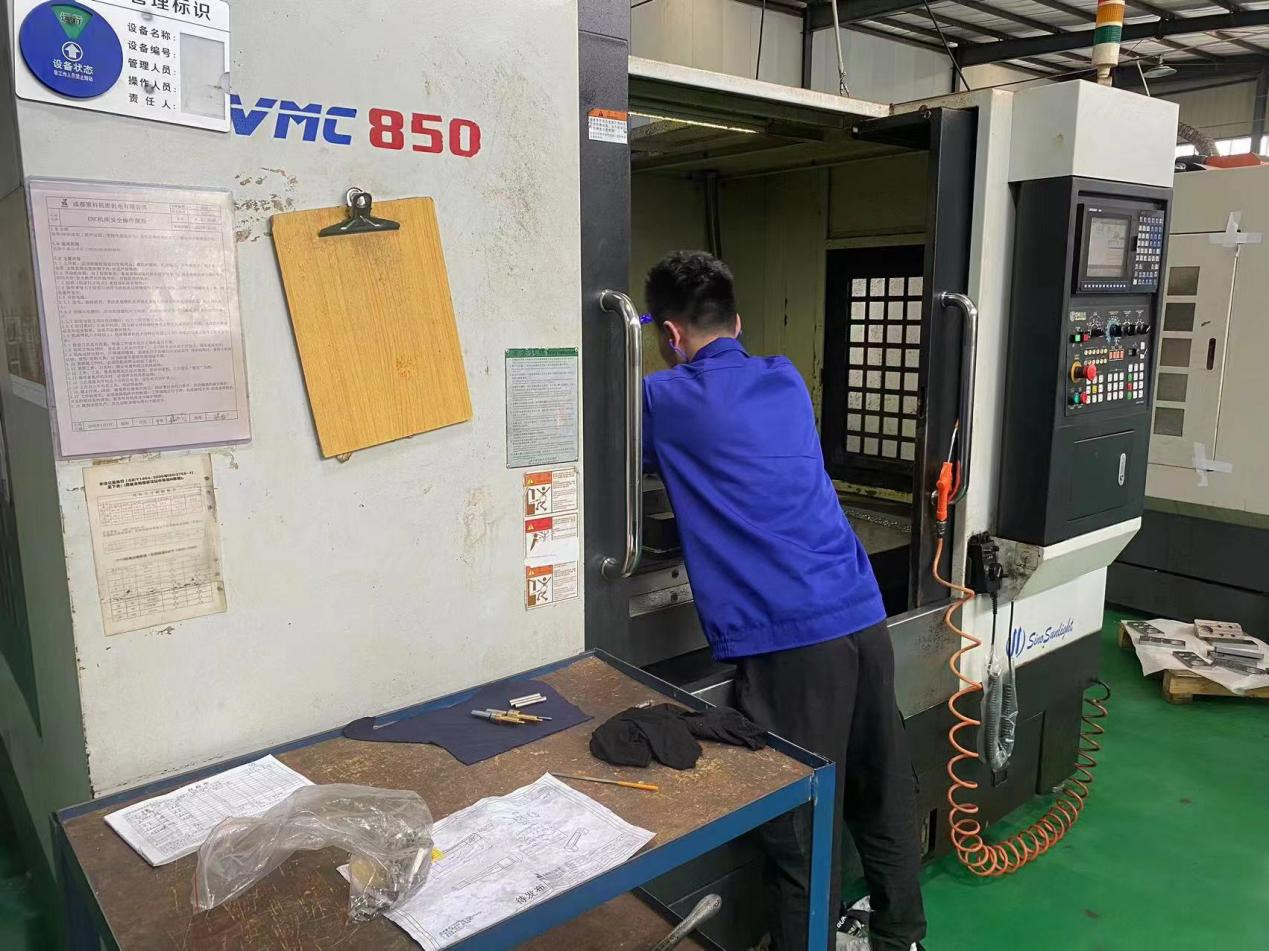
Was sind die Hauptfaktoren, die die Schnitzverarbeitung beeinflussen?
Die mechanische Bearbeitung ist ein relativ komplexer Prozess und wird von vielen Faktoren beeinflusst, darunter vor allem die folgenden: Werkzeugmaschineneigenschaften, Schneidwerkzeuge, Steuerungssysteme, Materialeigenschaften, Verarbeitungstechnologie, Hilfsvorrichtungen und Umgebung.
Welche Anforderungen werden an das Steuerungssystem bei der CNC-Gravurbearbeitung gestellt?
Die CNC-Gravurbearbeitung ist in erster Linie eine Fräsbearbeitung, daher muss das Steuerungssystem in der Lage sein, die Fräsbearbeitung zu steuern.Für die Bearbeitung kleiner Werkzeuge muss eine Feedforward-Funktion bereitgestellt werden, um den Weg im Voraus zu verlangsamen und die Häufigkeit von Werkzeugbrüchen zu verringern.Gleichzeitig ist es notwendig, die Schnittgeschwindigkeit in relativ glatten Bahnabschnitten zu erhöhen, um die Effizienz der Gravurbearbeitung zu verbessern.
Welche Materialeigenschaften beeinflussen die Verarbeitung?
Die Hauptfaktoren, die die Schnitzleistung von Materialien beeinflussen, sind Materialtyp, Härte und Zähigkeit.Die Materialkategorien umfassen metallische Werkstoffe und nichtmetallische Werkstoffe.Insgesamt gilt: Je höher die Härte, desto schlechter ist die Verarbeitbarkeit, während je höher die Viskosität, desto schlechter die Verarbeitbarkeit ist.Je mehr Verunreinigungen vorhanden sind, desto schlechter ist die Bearbeitbarkeit und desto größer ist die Härte der Partikel im Material, was zu einer schlechteren Bearbeitbarkeit führt.Ein allgemeiner Standard lautet: Je höher der Kohlenstoffgehalt, desto schlechter die Bearbeitbarkeit, je höher der Legierungsgehalt, desto schlechter die Bearbeitbarkeit und je höher der Gehalt an nichtmetallischen Elementen, desto besser die Bearbeitbarkeit (aber der nichtmetallische Gehalt im Allgemeinen). Materialien werden streng kontrolliert).
Welche Materialien eignen sich für die Schnitzbearbeitung?
Zu den zum Schnitzen geeigneten nichtmetallischen Materialien gehören organisches Glas, Harz, Holz usw. Zu den nicht zum Schnitzen geeigneten nichtmetallischen Materialien gehören natürlicher Marmor, Glas usw. Zu den zum Schnitzen geeigneten Metallmaterialien gehören Kupfer, Aluminium und weicher Stahl mit einer Härte von weniger als HRC40 , während ungeeignete Metallmaterialien zum Schnitzen vergüteter Stahl usw. sind.
Welchen Einfluss hat das Schneidwerkzeug selbst auf den Bearbeitungsprozess und wie beeinflusst es ihn?
Zu den Schneidwerkzeugfaktoren, die sich auf die Gravurverarbeitung auswirken, gehören Werkzeugmaterial, geometrische Parameter und Schleiftechnologie.Das bei der Schnitzbearbeitung verwendete Schneidwerkzeugmaterial ist Hartlegierungsmaterial, bei dem es sich um eine Pulverlegierung handelt.Der wichtigste Leistungsindikator, der die Materialleistung bestimmt, ist der durchschnittliche Durchmesser des Pulvers.Je kleiner der Durchmesser ist, desto verschleißfester ist das Werkzeug und desto höher ist die Lebensdauer des Werkzeugs.Weitere NC-Programmierkenntnisse konzentrieren sich auf das offizielle WeChat-Konto (NC-Programmierlehre), um das Tutorial zu erhalten.Die Schärfe des Werkzeugs beeinflusst hauptsächlich die Schnittkraft.Je schärfer das Werkzeug, desto geringer die Schnittkraft, desto gleichmäßiger die Bearbeitung und desto höher die Oberflächengüte, aber desto geringer die Haltbarkeit des Werkzeugs.Daher sollte bei der Bearbeitung unterschiedlicher Materialien eine unterschiedliche Schärfe gewählt werden.Bei der Bearbeitung weicher und klebriger Materialien ist ein Schärfen des Schneidwerkzeugs erforderlich.Wenn die Härte des bearbeiteten Materials hoch ist, sollte die Schärfe reduziert werden, um die Haltbarkeit des Schneidwerkzeugs zu verbessern.Es darf aber nicht zu stumpf sein, sonst wird die Schnittkraft zu groß und beeinträchtigt die Bearbeitung.Der entscheidende Faktor beim Werkzeugschleifen ist die Maschenweite der Präzisionsschleifscheibe.Eine hochmaschige Schleifscheibe kann feinere Schneidkanten erzeugen und so die Haltbarkeit des Schneidwerkzeugs effektiv verbessern.Schleifscheiben mit hoher Maschenweite können glattere Flankenoberflächen erzeugen, was die Oberflächenqualität beim Schneiden verbessern kann.
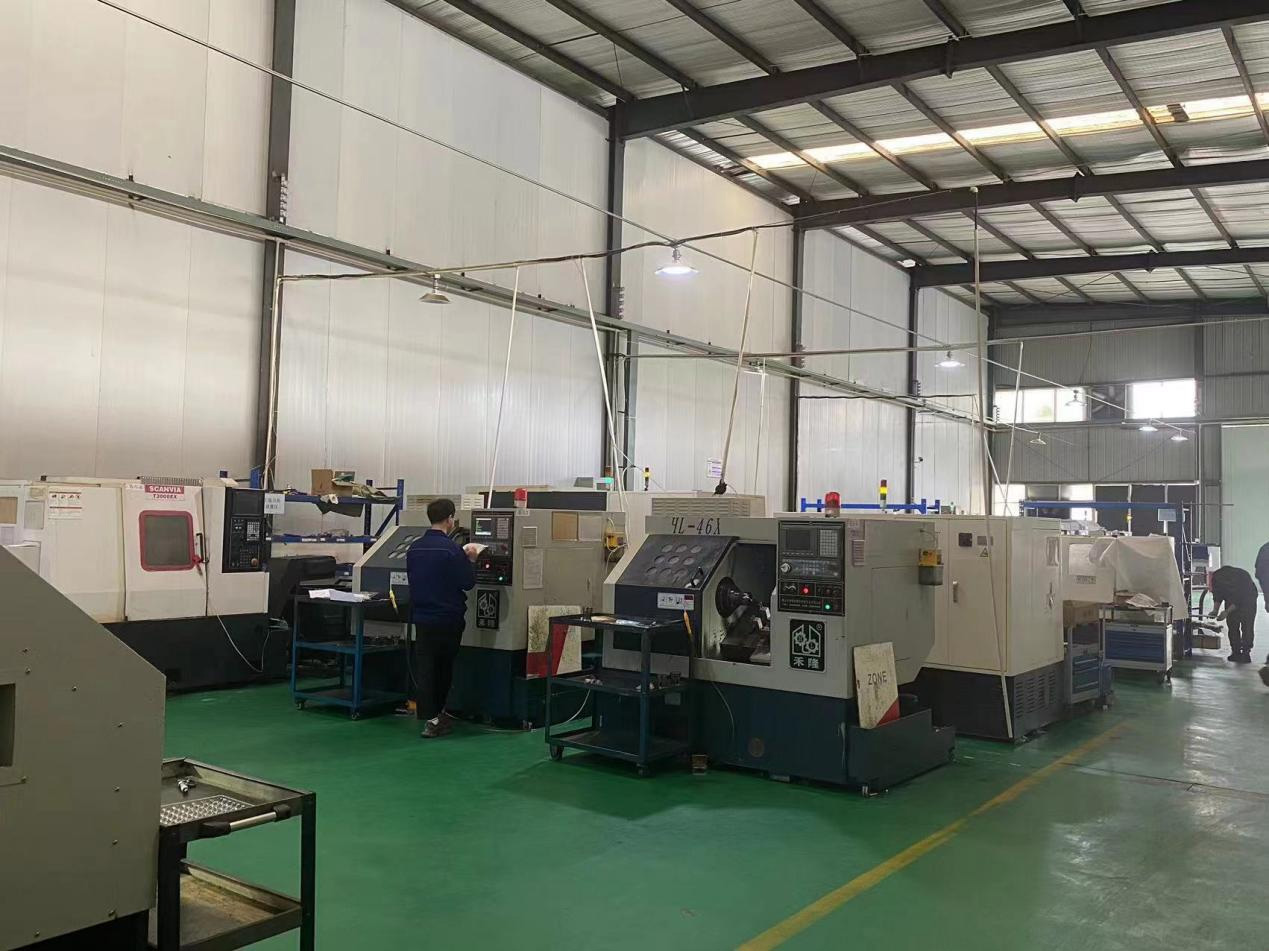
Wie lautet die Formel für die Werkzeugstandzeit?
Unter der Standzeit versteht man vor allem die Standzeit bei der Bearbeitung von Stahlwerkstoffen.Die empirische Formel lautet: (T ist die Standzeit des Werkzeugs, CT ist der Standzeitparameter, VC ist die Schnittliniengeschwindigkeit, f ist die Schnitttiefe pro Umdrehung und P ist die Schnitttiefe).Die Schnittliniengeschwindigkeit hat den größten Einfluss auf die Werkzeugstandzeit.Darüber hinaus können sich auch der Rundlauffehler des Werkzeugs, die Schleifqualität des Werkzeugs, das Werkzeugmaterial und die Beschichtung sowie das Kühlmittel auf die Haltbarkeit des Werkzeugs auswirken.
Wie schützt man die Ausrüstung der Schnitzmaschine während der Bearbeitung?
1) Schützen Sie das Werkzeugeinstellgerät vor übermäßiger Ölerosion.
2) Achten Sie auf die Kontrolle umherfliegender Trümmer.Umherfliegende Trümmer stellen eine große Gefahr für die Werkzeugmaschine dar.Ein Flug in den Schaltschrank kann zu einem Kurzschluss führen und ein Flug in die Führungsschiene kann die Lebensdauer von Schraube und Führungsschiene verkürzen.Daher sollten während der Bearbeitung die Hauptteile der Werkzeugmaschine ordnungsgemäß abgedichtet werden.
3) Ziehen Sie beim Bewegen der Beleuchtung nicht am Lampensockel, da der Lampensockel dadurch leicht beschädigt werden kann.
4) Nähern Sie sich während des Bearbeitungsprozesses nicht dem Schnittbereich, um ihn zu beobachten, um herumfliegende Trümmer zu vermeiden, die die Augen schädigen könnten.Bei rotierendem Spindelmotor ist es verboten, Arbeiten an der Werkbank durchzuführen.
5) Öffnen oder schließen Sie die Tür der Werkzeugmaschine beim Öffnen und Schließen nicht mit Gewalt.Bei der Präzisionsbearbeitung können durch Stöße und Vibrationen beim Türöffnungsvorgang Messerspuren auf der bearbeiteten Oberfläche entstehen.
6) Geben Sie die Spindeldrehzahl ein und starten Sie dann die Verarbeitung. Andernfalls wird aufgrund des langsamen Starts der Spindel möglicherweise nicht die gewünschte Geschwindigkeit erreicht, bevor mit der Verarbeitung begonnen wird, was dazu führt, dass der Motor erstickt.
7) Es ist verboten, Werkzeuge oder Werkstücke auf der Traverse der Werkzeugmaschine abzulegen.
8) Es ist strengstens verboten, magnetische Werkzeuge wie Magnetsaugnäpfe und Messuhrhalter auf dem Schaltschrank zu platzieren, da dies zu Schäden am Display führen kann.

Welche Funktion hat Schneidflüssigkeit?
Achten Sie bei der Metallbearbeitung auf die Zugabe von Kühlöl.Die Funktion des Kühlsystems besteht darin, die Schneidwärme und herumfliegende Späne abzuleiten und so für die Schmierung bei der Bearbeitung zu sorgen.Das Kühlmittel bewegt das Schneidband, reduziert die auf das Schneidwerkzeug und den Motor übertragene Wärme und verbessert deren Lebensdauer.Entfernen Sie umherfliegende Fremdkörper, um ein Nachschneiden zu vermeiden.Schmierung kann die Schnittkraft reduzieren und die Bearbeitung stabiler machen.Bei der Bearbeitung von Kupfer kann der Einsatz von ölhaltigem Kühlschmierstoff die Oberflächenqualität verbessern.
Welche Stadien des Werkzeugverschleißes gibt es?
Der Verschleiß von Schneidwerkzeugen lässt sich in drei Phasen einteilen: anfänglicher Verschleiß, normaler Verschleiß und scharfer Verschleiß.In der anfänglichen Verschleißphase liegt der Hauptgrund für den Werkzeugverschleiß darin, dass die Werkzeugtemperatur niedrig ist und nicht die optimale Schnitttemperatur erreicht.Zu diesem Zeitpunkt handelt es sich beim Werkzeugverschleiß hauptsächlich um abrasiven Verschleiß, der sich stärker auf das Werkzeug auswirkt.Weitere NC-Programmierkenntnisse konzentrieren sich auf das offizielle WeChat-Konto (Lehre in der Programmierung digitaler Steuerungen), um das Tutorial zu erhalten, das leicht zu Werkzeugbrüchen führen kann.Dieser Schritt ist sehr gefährlich und kann bei unsachgemäßer Handhabung direkt zum Bruch und Ausfall des Werkzeugs führen.Wenn das Werkzeug die anfängliche Verschleißphase durchläuft und die Schnitttemperatur einen bestimmten Wert erreicht, ist der Hauptverschleiß Diffusionsverschleiß, der hauptsächlich zu lokalem Abblättern führt.Der Verschleiß ist also relativ gering und langsam.Wenn der Verschleiß ein bestimmtes Maß erreicht, wird das Werkzeug wirkungslos und tritt in eine Phase schnellen Verschleißes ein.
Warum und wie müssen Schneidwerkzeuge eingefahren werden?
Wir haben oben erwähnt, dass das Werkzeug in der anfänglichen Verschleißphase anfällig für Brüche ist.Um das Phänomen des Bruchs zu vermeiden, müssen wir das Werkzeug einfahren.Erhöhen Sie die Schneidtemperatur des Werkzeugs schrittweise auf eine angemessene Temperatur.Nach experimenteller Verifizierung wurden Vergleiche mit den gleichen Verarbeitungsparametern durchgeführt.Man erkennt, dass sich die Werkzeugstandzeit nach dem Einlaufen um mehr als das Doppelte erhöht hat.
Die Einlaufmethode besteht darin, die Vorschubgeschwindigkeit unter Beibehaltung einer angemessenen Spindeldrehzahl um die Hälfte zu reduzieren. Die Bearbeitungszeit beträgt etwa 5 bis 10 Minuten.Nehmen Sie bei der Bearbeitung weicher Materialien den kleinen Wert, bei der Bearbeitung harter Metalle den großen Wert.
Wie lässt sich starker Werkzeugverschleiß feststellen?
Die Methode zur Bestimmung des starken Werkzeugverschleißes ist:
1) Hören Sie sich das Verarbeitungsgeräusch an und machen Sie einen scharfen Anruf;
2) Beim Hören des Geräusches der Spindel fällt auf, dass sich die Spindel zurückhält;
3) Gefühl, dass die Vibrationen während der Bearbeitung zunehmen und es zu deutlichen Vibrationen an der Werkzeugmaschinenspindel kommt;
4) Aufgrund des Bearbeitungseffekts kann das bearbeitete Untermessermuster gut oder schlecht sein (wenn dies am Anfang der Fall ist, deutet dies darauf hin, dass die Schnitttiefe zu tief ist).
Wann sollte ich das Messer wechseln?
Wir sollten das Werkzeug nach etwa 2/3 der Standzeitgrenze austauschen.Wenn das Werkzeug beispielsweise innerhalb von 60 Minuten starken Verschleiß erfährt, sollte die nächste Bearbeitung innerhalb von 40 Minuten mit dem Werkzeugwechsel beginnen und sich angewöhnen, das Werkzeug regelmäßig zu wechseln.
Können stark verschlissene Werkzeuge weiter bearbeitet werden?
Nach starkem Werkzeugverschleiß kann die Schnittkraft auf das Dreifache des Normalwerts ansteigen.Die Schnittkraft hat einen erheblichen Einfluss auf die Lebensdauer der Spindelelektrode, und das Verhältnis zwischen der Lebensdauer des Spindelmotors und der Kraft ist umgekehrt proportional zur dritten Potenz.Wenn sich beispielsweise die Schnittkraft um das Dreifache erhöht, entspricht eine Bearbeitungszeit von 10 Minuten einer Verwendung der Spindel für 10 * 33 = 270 Minuten unter normalen Bedingungen.
Wie ermittelt man die Ausfahrlänge des Werkzeugs bei der Grobbearbeitung?
Je kürzer die Auszugslänge des Werkzeugs, desto besser.Wenn es jedoch bei der tatsächlichen Bearbeitung zu kurz ist, muss die Länge des Werkzeugs häufig angepasst werden, was die Bearbeitungseffizienz stark beeinträchtigen kann.Wie sollte also die Ausfahrlänge des Schneidwerkzeugs bei der tatsächlichen Bearbeitung gesteuert werden?Das Prinzip ist wie folgt: φ Eine Werkzeugstange mit einem Durchmesser von 3 kann durch Verlängerung um 5 mm normal bearbeitet werden.φ Der Mähbalken mit 4 Durchmessern kann durch Ausfahren um 7 mm normal bearbeitet werden.φ Der Mähbalken mit 6 Durchmessern kann durch eine Verlängerung um 10 mm normal bearbeitet werden.Versuchen Sie beim Schneiden, diese Werte zu unterschreiten.Wenn die Länge des Oberwerkzeugs größer als der oben genannte Wert ist, versuchen Sie, die Bearbeitungstiefe bei Werkzeugverschleiß zu kontrollieren.Das ist etwas schwer zu verstehen und erfordert mehr Übung.
Wie gehe ich mit einem plötzlichen Werkzeugbruch während der Bearbeitung um?
1) Stoppen Sie die Bearbeitung und sehen Sie sich die aktuelle Seriennummer der Bearbeitung an.
2) Überprüfen Sie, ob an der Schneidstelle eine gebrochene Klinge vorhanden ist, und entfernen Sie diese gegebenenfalls.
3) Analysieren Sie die Ursache des kaputten Werkzeugs, was am wichtigsten ist.Warum ist das Werkzeug kaputt gegangen?Wir müssen die oben genannten verschiedenen Faktoren analysieren, die sich auf die Verarbeitung auswirken.Der Grund für den Bruch des Werkzeugs liegt jedoch darin, dass die auf das Werkzeug einwirkende Kraft plötzlich zunimmt.Entweder handelt es sich um ein Pfadproblem, das Werkzeug wackelt übermäßig, das Material enthält harte Blöcke oder die Drehzahl des Spindelmotors ist falsch.
4) Ersetzen Sie nach der Analyse das Werkzeug zur Bearbeitung.Wenn der Pfad nicht geändert wurde, sollte die Bearbeitung eine Nummer vor der ursprünglichen Nummer erfolgen.Zu diesem Zeitpunkt muss auf eine Reduzierung der Vorschubgeschwindigkeit geachtet werden.Dies liegt daran, dass die Verhärtung beim Werkzeugbruch stark ist und außerdem ein Einfahren des Werkzeugs erforderlich ist.
Wie können Bearbeitungsparameter angepasst werden, wenn die Grobbearbeitung nicht gut ist?
Wenn die Werkzeugstandzeit bei einer angemessenen Hauptachsengeschwindigkeit nicht garantiert werden kann, passen Sie beim Anpassen der Parameter zuerst die Schnitttiefe, dann die Vorschubgeschwindigkeit und dann erneut die seitliche Vorschubgeschwindigkeit an.(Hinweis: Auch das Anpassen der Schnitttiefe weist Einschränkungen auf. Wenn die Schnitttiefe zu gering ist und zu viele Schichten vorhanden sind, kann die theoretische Schnitteffizienz hoch sein. Die tatsächliche Verarbeitungseffizienz wird jedoch durch andere Faktoren beeinflusst, was zu einer zu geringen Verarbeitung führt Effizienz. An diesem Punkt ist es notwendig, das Schneidwerkzeug für die Bearbeitung durch ein kleineres zu ersetzen, aber die Bearbeitungseffizienz ist höher. Im Allgemeinen darf die minimale Schnitttiefe nicht weniger als 0,1 mm betragen.
Zeitpunkt der Veröffentlichung: 13. April 2023