Гравірувальні верстати з ЧПК підходять для точної обробки за допомогою невеликих інструментів і володіють здатністю фрезерування, шліфування, свердління та високошвидкісного нарізування.Вони широко використовуються в різних галузях, таких як промисловість 3C, промисловість форм і медична промисловість.У цій статті зібрано поширені запитання про обробку гравіювання з ЧПУ.
Які основні відмінності між гравіруванням і фрезеруванням?
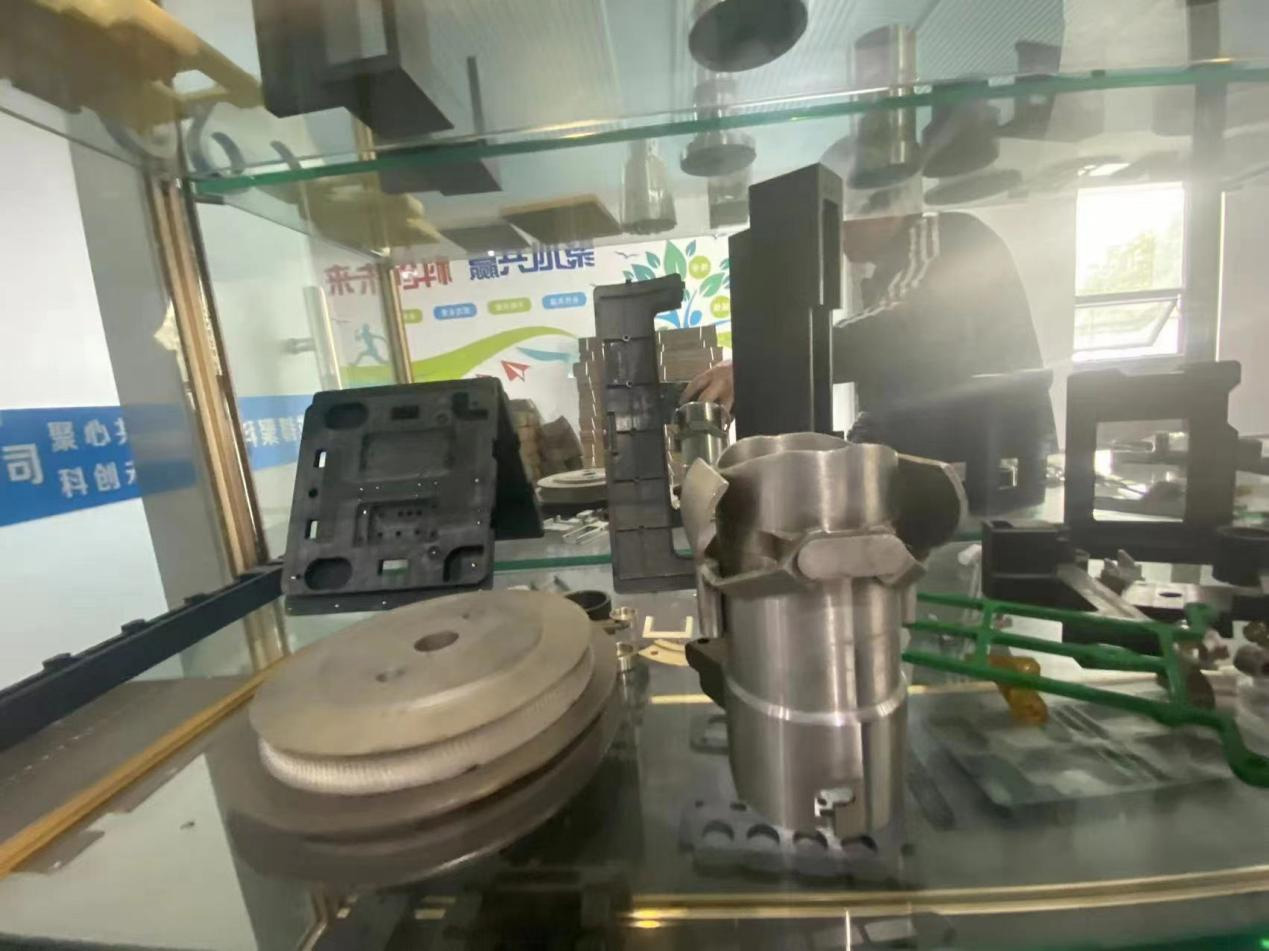
Процеси гравірування та фрезерування з ЧПК використовують принципи фрезерування.Основна відмінність полягає в використовуваному діаметрі інструменту, причому для фрезерування з ЧПК зазвичай використовується діапазон діаметрів інструментів від 6 до 40 міліметрів, тоді як діаметр інструментів для обробки гравіювання з ЧПК коливається від 0,2 до 3 міліметрів.
Чи може фрезерування з ЧПУ використовуватися лише для чорної обробки, а гравірування з ЧПУ – лише для точної обробки?
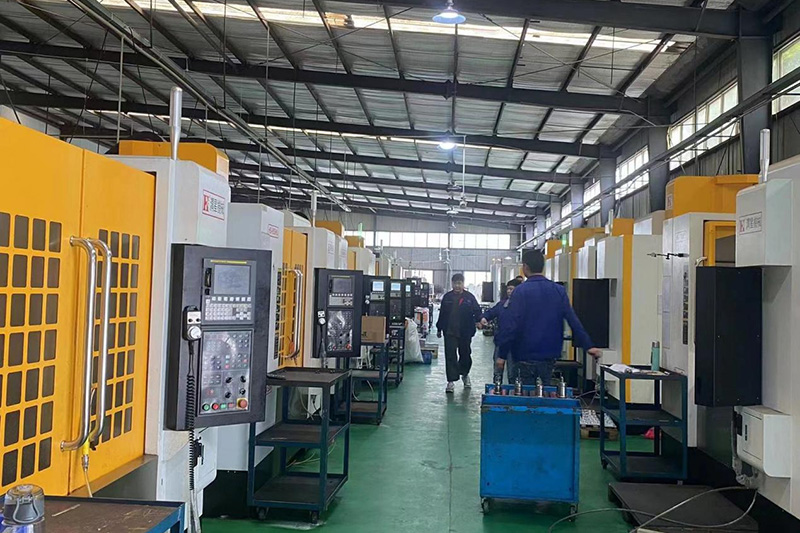
Перш ніж відповісти на це питання, давайте спочатку розберемося з концепцією процесу.Обсяг обробки грубої обробки великий, тоді як обсяг обробки точної обробки невеликий, тому деякі люди зазвичай вважають чорнову обробку "важким різанням", а точну обробку - "легким різанням".Насправді груба обробка, напівточна обробка та точна обробка — це концепції процесу, які представляють різні етапи обробки.Отже, точна відповідь на це запитання полягає в тому, що фрезерування з ЧПК може виконувати важке різання або легке різання, тоді як гравірування з ЧПК може виконувати лише легке різання.
Чи можна використовувати процес гравірування з ЧПК для грубої обробки сталевих матеріалів?
Вирішення того, чи можна гравіюванням з ЧПК обробити певний матеріал, в основному залежить від того, наскільки великий інструмент можна використовувати.Ріжучі інструменти, які використовуються при обробці гравірування з ЧПУ, визначають його максимальну різальну здатність.Якщо форма прес-форми дозволяє використовувати інструменти діаметром понад 6 міліметрів, настійно рекомендується спочатку використовувати фрезерування з ЧПУ, а потім використовувати різьблення, щоб видалити залишки матеріалу.
Чи може додавання головки зі збільшенням швидкості до шпинделя обробного центру з ЧПК завершити обробку гравіювання?
Не вдалося завершити.Цей виріб з’явився на виставці два роки тому, але завершити процес різьблення не вдалося.Основна причина полягає в тому, що конструкція обробних центрів з ЧПК враховує власний діапазон інструментів, а загальна структура не підходить для обробки гравіюванням.Основна причина цієї помилкової ідеї полягає в тому, що вони помилково прийняли високошвидкісний електричний шпиндель як єдину функцію гравірувального верстата.
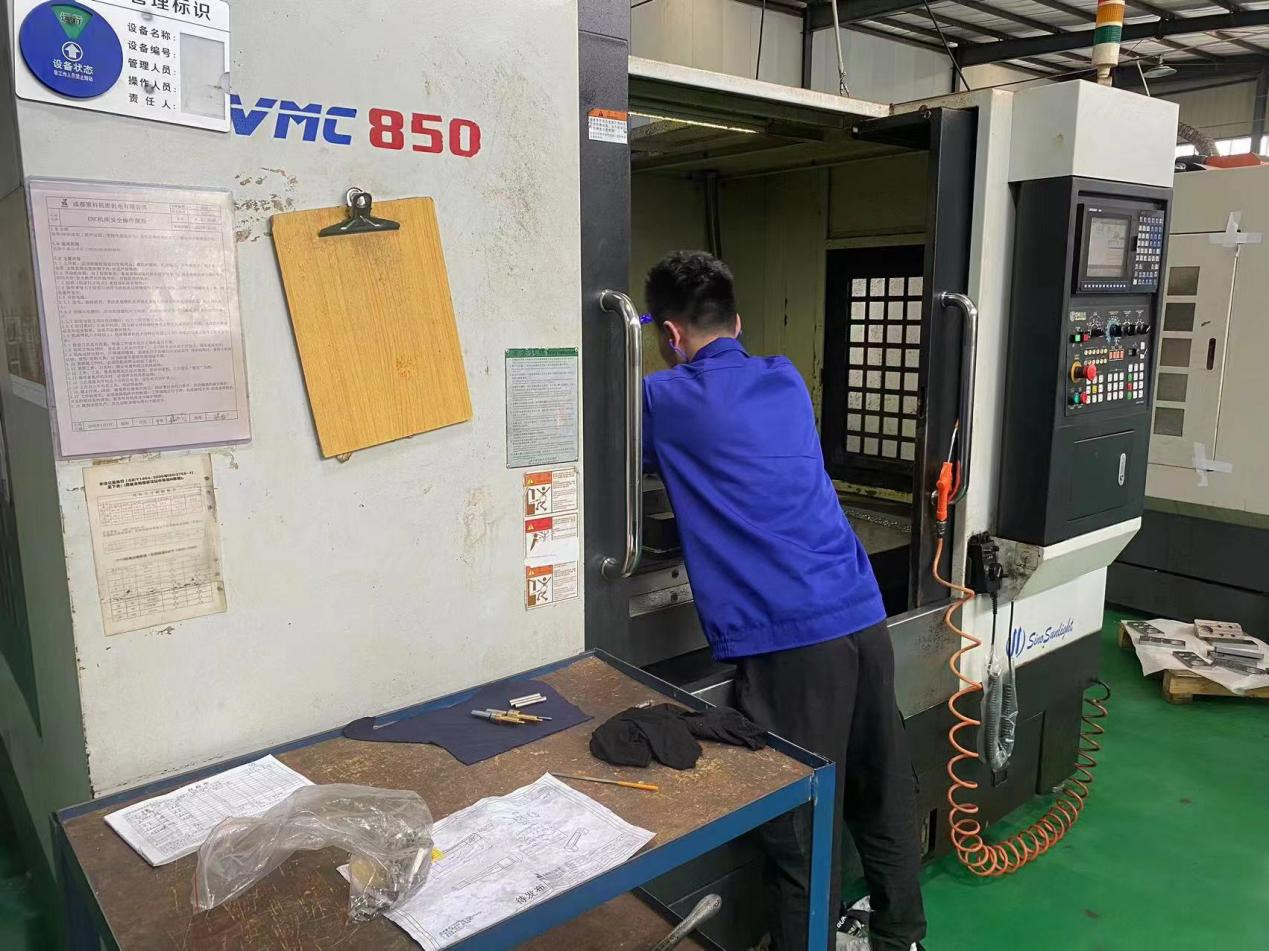
Які основні фактори впливають на обробку різьбою?
Механічна обробка є відносно складним процесом, і існує багато факторів, які впливають на неї, в основному включаючи такі: характеристики верстатів, ріжучі інструменти, системи керування, характеристики матеріалу, технологія обробки, допоміжні пристосування та навколишнє середовище.
Які вимоги до системи керування при обробці гравіювання з ЧПУ?
Обробка гравіювання з ЧПУ - це в основному фрезерна обробка, тому система керування повинна мати можливість контролювати фрезерну обробку.Для обробки невеликих інструментів необхідно передбачити функцію прямої подачі, щоб завчасно уповільнити шлях і зменшити частоту поломки інструменту.У той же час необхідно збільшити швидкість різання на відносно гладких ділянках шляху, щоб підвищити ефективність обробки гравіювання.
Які характеристики матеріалів впливатимуть на обробку?
Основними факторами, що впливають на характеристики різьблення матеріалів, є тип матеріалу, твердість і в’язкість.Категорії матеріалів включають металеві та неметалеві матеріали.Загалом, чим вища твердість, тим гірша оброблюваність, а чим вища в’язкість, тим гірша оброблюваність.Чим більше домішок, тим гірша оброблюваність і тим більша твердість частинок усередині матеріалу, що призводить до гіршої оброблюваності.Загальний стандарт такий: чим вищий вміст вуглецю, тим гірша оброблюваність, чим вищий вміст сплаву, тим гірша оброблюваність, а чим вищий вміст неметалічних елементів, тим краща оброблюваність (але вміст неметалів загалом матеріали суворо контролюються).
Які матеріали підходять для обробки різьбою?
Неметалевими матеріалами, придатними для різьблення, є органічне скло, смола, дерево тощо. Неметалевими матеріалами, непридатними для різьблення, є натуральний мармур, скло тощо. До придатних металевих матеріалів для різьблення належать мідь, алюміній і м’яка сталь із твердістю менше HRC40. , тоді як непридатні металеві матеріали для різьблення включають загартовану сталь тощо.
Який вплив самого ріжучого інструменту на процес обробки і як він на нього впливає?
Фактори ріжучого інструменту, які впливають на обробку гравірування, включають матеріал інструменту, геометричні параметри та технологію шліфування.Матеріал ріжучого інструменту, який використовується для обробки різьблення, - це твердий сплав, який є порошковим сплавом.Основним показником ефективності, що визначає продуктивність матеріалу, є середній діаметр порошку.Чим менший діаметр, тим більш зносостійкий інструмент, і тим вище буде його довговічність.Більше знань про програмування NC зосереджено на офіційному обліковому записі WeChat (навчання програмуванню NC), щоб отримати підручник.На силу різання в основному впливає гострота інструменту.Чим гостріший інструмент, тим менша сила різання, плавніша обробка і вища якість поверхні, але менша довговічність інструменту.Тому при обробці різних матеріалів слід підбирати різну різкість.При обробці м'яких і липких матеріалів необхідно заточувати ріжучий інструмент.Коли твердість оброблюваного матеріалу висока, гостроту слід зменшити, щоб підвищити довговічність ріжучого інструменту.Але він не може бути занадто тупим, інакше сила різання буде занадто великою та вплине на обробку.Ключовим фактором при шліфуванні інструменту є розмір отвору точного шліфувального круга.Шліфувальний круг із високим вічком може створювати більш тонкі ріжучі кромки, ефективно покращуючи довговічність ріжучого інструменту.Шліфувальні круги з великим розміром отвору можуть створювати більш гладкі бічні поверхні, що може покращити якість поверхні різання.
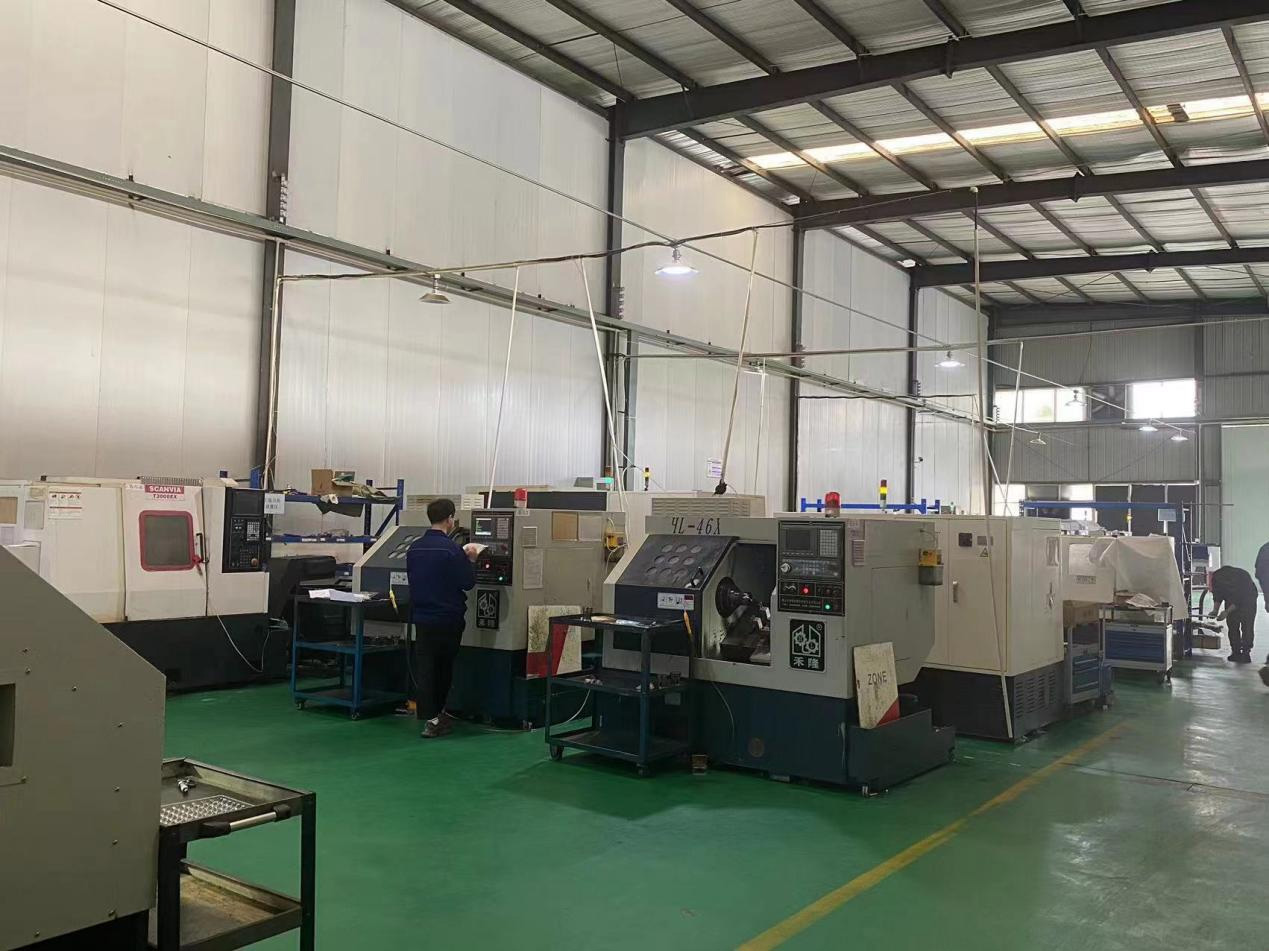
Яка формула довговічності інструменту?
Стійкість інструменту в основному відноситься до довговічності інструменту під час обробки сталевих матеріалів.Емпірична формула: (T — довговічність інструменту, CT — параметр довговічності, VC — швидкість лінії різання, f — глибина різання на один оберт, P — глибина різання).Швидкість лінії різання найбільше впливає на термін служби інструменту.Крім того, радіальне биття інструменту, якість шліфування інструменту, матеріал інструменту та покриття, а також охолоджуюча рідина також можуть впливати на довговічність інструменту.
Як захистити обладнання верстатів для різьблення під час обробки?
1) Захистіть пристрій для налаштування інструменту від надмірної ерозії масла.
2) Зверніть увагу на контроль над летючими уламками.Літаючі уламки представляють велику загрозу для верстата.Влітання в електричну шафу керування може спричинити коротке замикання, а влітання в напрямну може зменшити термін служби гвинта та напрямної.Тому під час обробки основні частини верстата повинні бути належним чином ущільнені.
3) Під час переміщення освітлення не тягніть за цоколь лампи, оскільки це може легко пошкодити цоколь лампи.
4) Під час процесу обробки не наближайтеся до зони різання для спостереження, щоб уникнути розльоту сміття, яке може пошкодити очі.Коли двигун шпинделя обертається, забороняється виконувати будь-які операції на верстаку.
5) Відкриваючи та закриваючи дверцята верстата, не відкривайте та не закривайте їх із силою.Під час точної обробки удар і вібрація під час відкривання дверей можуть спричинити сліди від ножа на обробленій поверхні.
6) Надати швидкості шпинделя, а потім почати обробку, інакше через повільний запуск шпинделя бажана швидкість може не досягнутися до початку обробки, в результаті чого двигун задихнеться.
7) Забороняється розташовувати будь-які інструменти або заготовки на поперечині верстата.
8) Категорично заборонено розміщувати магнітні інструменти, такі як магнітні присоски та тримачі циферблатного індикатора, на електричній шафі керування, оскільки це може пошкодити дисплей.

Яка функція ріжучої рідини?
Зверніть увагу на додавання охолоджуючої олії під час обробки металу.Функція системи охолодження полягає у видаленні тепла різання та летючого сміття, забезпечуючи змащення для обробки.Охолоджувальна рідина буде рухати ріжучий ремінь, зменшуючи тепло, що передається ріжучому інструменту та двигуну, і подовжуючи їх термін служби.Приберіть сміття, що летить, щоб уникнути вторинного різання.Змащення може зменшити силу різання та зробити обробку більш стабільною.Під час обробки міді використання масляної рідини для різання може покращити якість поверхні.
Які стадії зносу інструменту?
Знос різальних інструментів можна розділити на три стадії: початковий знос, нормальний знос і різкий знос.На початковій стадії зносу основною причиною зносу інструменту є низька температура інструменту, яка не досягає оптимальної температури різання.У цей час знос інструменту є в основному абразивним, що має більший вплив на інструмент.Більше знань про програмування NC зосереджено на офіційному обліковому записі WeChat (навчання програмуванню цифрового керування), щоб отримати підручник, який легко спричинити поломку інструменту.Цей етап дуже небезпечний, і якщо не поводитися належним чином, він може безпосередньо призвести до поломки інструменту та виходу з ладу.Коли інструмент проходить початковий період зносу і температура різання досягає певного значення, основним зносом є дифузійний знос, який в основному викликає місцеве відшарування.Таким чином, знос відносно невеликий і повільний.Коли знос досягає певного рівня, інструмент стає неефективним і переходить у період швидкого зносу.
Чому і як потрібно обкатувати ріжучі інструменти?
Вище ми згадували, що на початковій стадії зносу інструмент схильний до поломки.Щоб уникнути явища поломки, ми повинні запустити інструмент.Поступово збільшуйте температуру різання інструментом до розумної температури.Після експериментальної перевірки було проведено порівняння з використанням однакових параметрів обробки.Видно, що після обкатки ресурс інструменту збільшився більш ніж вдвічі.
Спосіб обкатки полягає в зниженні швидкості подачі вдвічі при збереженні прийнятної швидкості шпинделя, а час обробки становить приблизно 5-10 хвилин.При обробці м'яких матеріалів беріть мале значення, а при обробці твердих металів - велике.
Як визначити сильний знос інструменту?
Метод визначення сильного зносу інструменту:
1) Послухайте звук обробки та зробіть різкий виклик;
2) Прислухаючись до звуку веретена, помітно явище затримки веретена;
3) Відчуття, що вібрація збільшується під час обробки, і є очевидна вібрація на шпинделі верстата;
4) Залежно від ефекту обробки оброблений малюнок нижнього леза може бути хорошим або поганим (якщо це так на початку, це означає, що глибина різання занадто велика).
Коли міняти ніж?
Ми повинні замінити інструмент приблизно на 2/3 терміну служби інструменту.Наприклад, якщо інструмент сильно зношується протягом 60 хвилин, наступну обробку слід почати змінювати протягом 40 хвилин і виробити звичку регулярно міняти інструмент.
Чи можна продовжувати обробляти сильно зношені інструменти?
Після сильного зносу інструменту сила різання може зрости втричі.Зусилля різання має значний вплив на термін служби електрода шпинделя, а залежність між терміном служби двигуна шпинделя та силою обернено пропорційна третьому ступені.Наприклад, коли сила різання збільшується втричі, обробка протягом 10 хвилин еквівалентна використанню шпинделя протягом 10 * 33 = 270 хвилин за нормальних умов.
Як визначити довжину подовження інструменту під час чорнової обробки?
Чим менша довжина розширення інструменту, тим краще.Однак під час фактичної обробки, якщо він занадто короткий, довжину інструменту потрібно часто регулювати, що може значно вплинути на ефективність обробки.Отже, як слід контролювати довжину подовження ріжучого інструменту під час фактичної обробки?Принцип такий: φ Панель інструментів діаметром 3 можна нормально обробити, подовжуючи її на 5 мм.φ Ріжучий брус діаметром 4 діаметра можна нормально обробляти, подовжуючи його на 7 мм.φ Ріжучу планку діаметром 6 діаметрів можна нормально обробляти, подовжуючи її на 10 мм.Спробуйте досягти нижче цих значень під час різання.Якщо довжина верхнього інструменту більша за вказане вище значення, спробуйте контролювати її на глибину обробки при зносі інструменту.Це трохи складно зрозуміти і потребує додаткового навчання.
Як впоратися з раптовою поломкою інструменту під час обробки?
1) Зупиніть обробку та перегляньте поточний серійний номер обробки.
2) Перевірте, чи немає зламаного леза в місці різання, і якщо так, видаліть його.
3) Проаналізуйте причину поломки інструменту, яка є найважливішою.Чому зламався інструмент?Нам потрібно проаналізувати різні фактори, які впливають на обробку, згадану вище.Але причина зламаного інструменту полягає в тому, що зусилля на інструмент раптово збільшується.Або це проблема траєкторії, або є надмірне тремтіння інструменту, або в матеріалі є жорсткі блоки, або швидкість двигуна шпинделя неправильна.
4) Після аналізу замініть інструмент для обробки.Якщо траєкторія не була змінена, обробку слід виконувати на один номер вперед від вихідного номера.У цей час необхідно звернути увагу на зниження швидкості подачі.Це пов'язано з тим, що зміцнення на зламі інструменту є сильним, а також необхідно виконати обкатку інструменту.
Як налаштувати параметри обробки, коли груба обробка не підходить?
Якщо термін служби інструменту не може бути гарантований при прийнятній швидкості головної осі, під час налаштування параметрів спочатку відрегулюйте глибину різання, потім відрегулюйте швидкість подачі, а потім знову відрегулюйте швидкість бічної подачі.(Примітка: Регулювання глибини різання також має обмеження. Якщо глибина різання замала і є забагато шарів, теоретична ефективність різання може бути високою. Однак на фактичну ефективність обробки впливають інші фактори, що призводить до занадто низької обробки ефективність. На цьому етапі необхідно замінити ріжучий інструмент на менший для обробки, але ефективність обробки буде вищою. Загалом, мінімальна глибина різання не може бути менше 0,1 мм.).
Час публікації: 13 квітня 2023 р