CNC оюу машиналары кичинекей шаймандар менен так иштетүүдө чебер жана фрезерлөө, майдалоо, бургулоо жана жогорку ылдамдыкта таптатуу жөндөмүнө ээ.Алар 3C өнөр жайы, көк өнөр жайы жана медициналык өнөр жайы сыяктуу ар кандай тармактарда кеңири колдонулат.Бул макалада CNC оюп иштетүү боюнча жалпы суроолорду чогултат.
CNC оюу менен CNC фрезеринин негизги айырмачылыктары эмнеде?
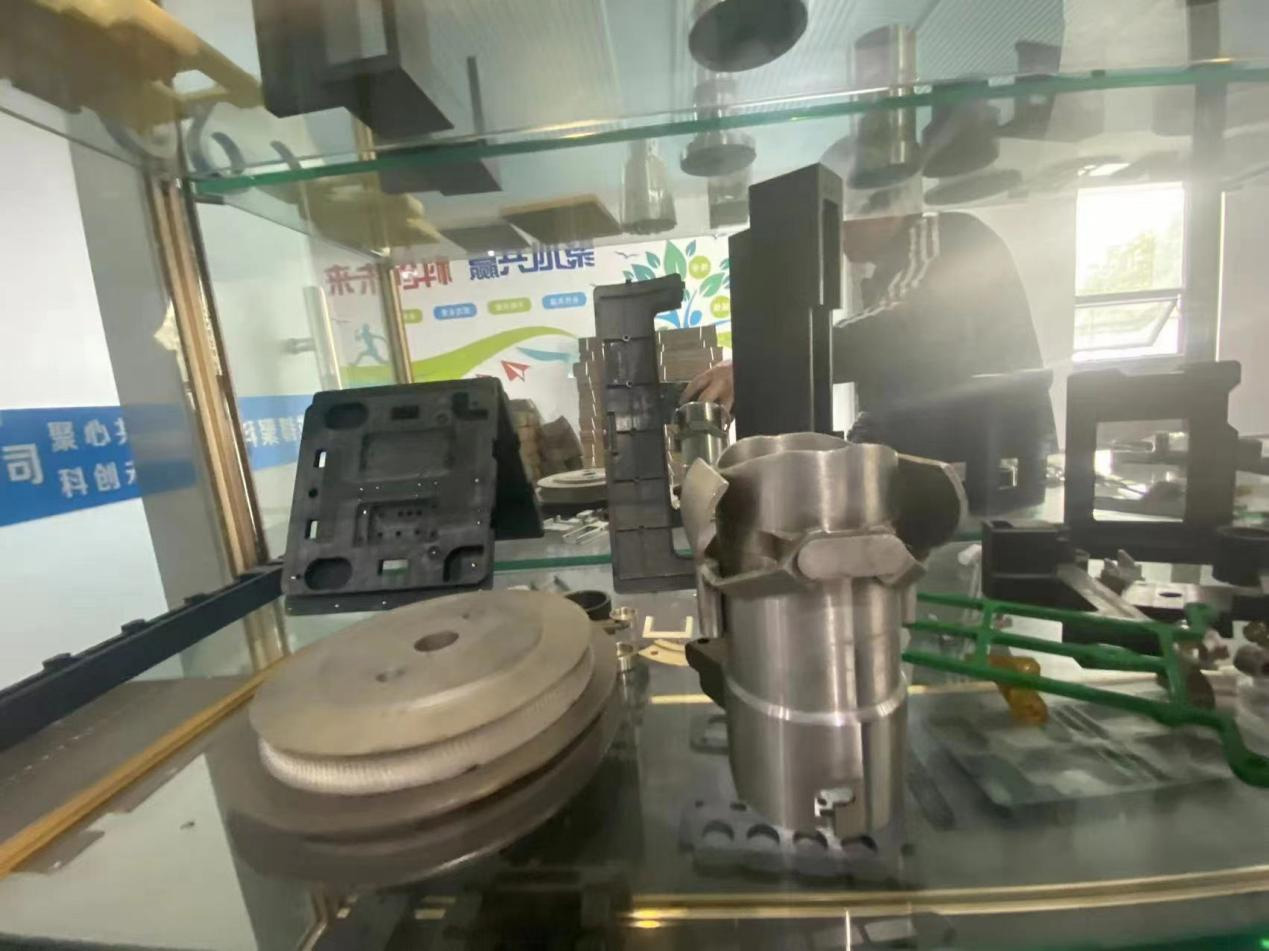
CNC оюу жана CNC фрезерлөө процесстери фрезерлөө принциптерин колдонушат.Негизги айырмачылык колдонулган аспаптын диаметринде, CNC фрезерлөө үчүн кеңири колдонулган инструмент диаметри диапазону 6дан 40 миллиметрге чейин, ал эми CNC гравюра иштетүү үчүн инструмент диаметри 0,2ден 3 миллиметрге чейин.
CNC фрезаны орой иштетүү үчүн гана колдонсо болобу, ал эми CNC оюу тактык иштетүү үчүн гана колдонулушу мүмкүнбү?
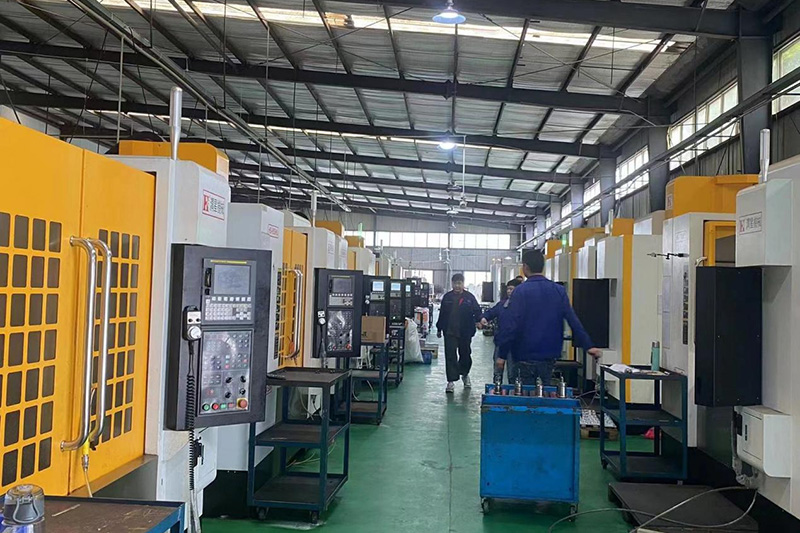
Бул суроого жооп берүүдөн мурун, алгач процесстин түшүнүгүн түшүнүп алалы.Орой иштетүүнүн иштетүү көлөмү чоң, ал эми так иштетүүнүн көлөмү аз, ошондуктан кээ бир адамдар одоно иштетүүнү "оор кесүү", ал эми так иштетүүнү "жеңил кесүү" деп эсептешет.Чынында, орой иштетүү, жарым тактык иштетүү жана так иштетүү ар кандай иштетүү этаптарын чагылдырган процесс түшүнүктөр.Ошентип, бул суроого так жооп, CNC фрезасы оор кесүүнү же жеңил кесүүнү жасай алат, ал эми CNC гравировкасы жеңил кесүүнү гана жасай алат.
CNC оюу процесси болоттон жасалган материалдарды орой иштетүү үчүн колдонулушу мүмкүнбү?
CNC гравюрасынын белгилүү бир материалды иштете алабы же жокпу, негизинен куралдын канчалык чоңдугуна жараша болот.CNC оюп иштетүүдө колдонулган кесүүчү аспаптар анын максималдуу кесүү жөндөмдүүлүгүн аныктайт.Эгерде калыптын формасы диаметри 6 миллиметрден ашкан инструменттерди колдонууга мүмкүндүк берсе, анда алгач CNC фрезаны колдонуу, андан кийин калган материалды алып салуу үчүн оюмду колдонуу катуу сунушталат.
CNC иштетүү борборунун шпинделине ылдамдыкты жогорулатуучу башты кошуу оюп иштетүүнү аягына чыгара алабы?
Аяктоо мүмкүн эмес.Бул буюм эки жыл мурун көргөзмөдө пайда болгон, бирок оюп бүтүрүү мүмкүн болгон эмес.Негизги себеби, CNC иштетүү борборлорунун дизайны өздөрүнүн инструменттеринин диапазонун карап, жалпы структурасы оюп иштетүү үчүн ылайыктуу эмес.Мындай жаңылыш ойдун негизги себеби, алар жогорку ылдамдыктагы электр шпиндельди оюу машинасынын бирден-бир өзгөчөлүгү катары кабыл алышкан.
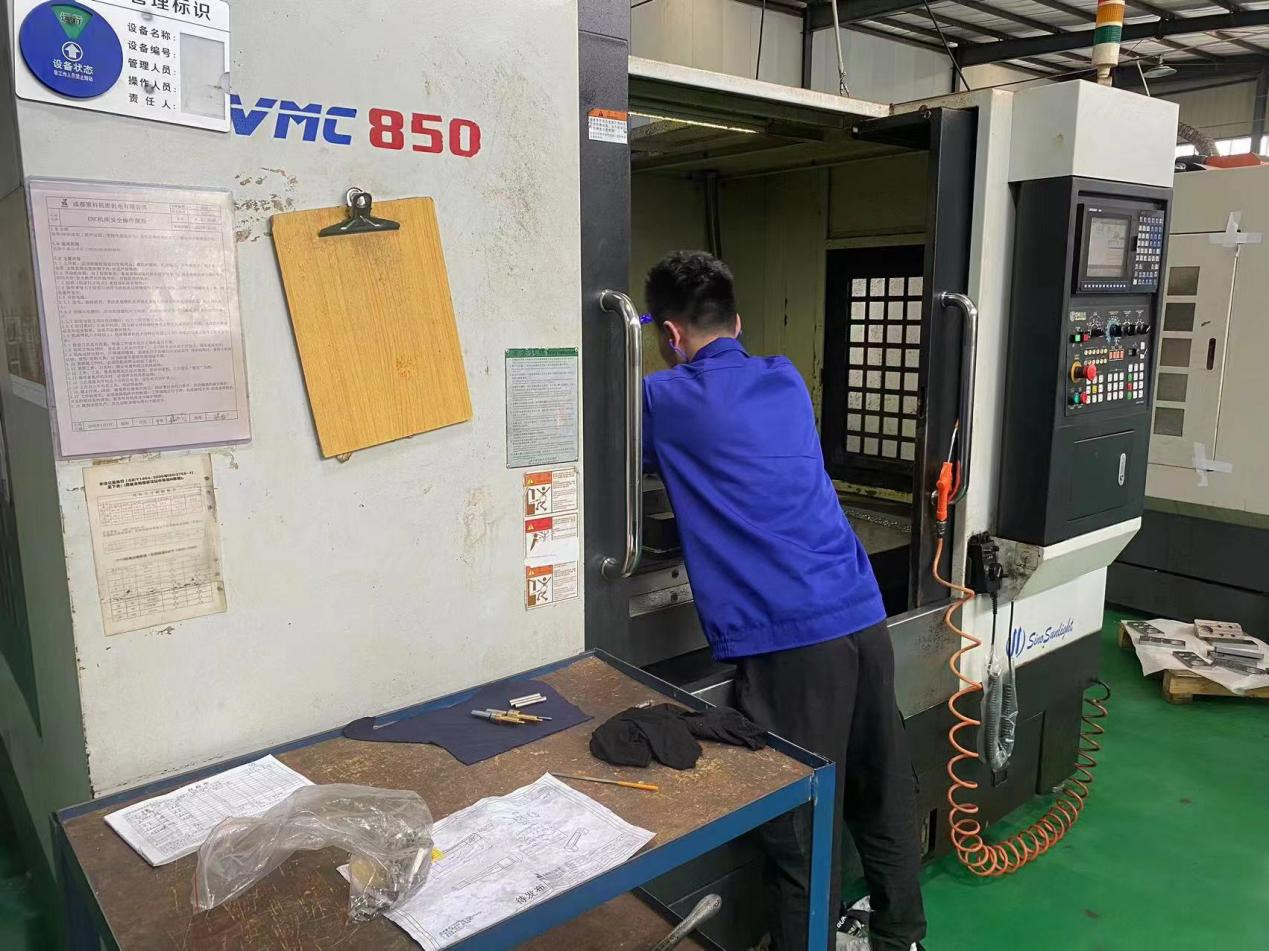
Оймо иштетүүгө кандай негизги факторлор таасир этет?
Механикалык иштетүү салыштырмалуу татаал процесс болуп саналат жана ага таасир этүүчү көптөгөн факторлор бар, анын ичинде төмөнкүлөр: станоктун мүнөздөмөлөрү, кесүүчү шаймандар, башкаруу системалары, материалдык мүнөздөмөлөр, иштетүү технологиясы, көмөкчү шаймандар жана айлана-чөйрө.
CNC оюп иштетүүдө башкаруу системасына кандай талаптар коюлат?
CNC оюп иштетүү, биринчи кезекте, фрезерлөө болуп саналат, ошондуктан башкаруу системасы фрезерлөө иштетүүнү көзөмөлдөө мүмкүнчүлүгүнө ээ болушу керек.Чакан инструментти иштетүү үчүн алдын ала жолду басаңдатуу жана инструменттин бузулуу жыштыгын азайтуу үчүн алдыга багыттоо функциясы камсыз кылынышы керек.Ошол эле учурда, оюп иштетүүнүн натыйжалуулугун жогорулатуу үчүн, салыштырмалуу жылмакай жол сегменттеринде кесүү ылдамдыгын жогорулатуу зарыл.
Материалдардын кандай мүнөздөмөлөрү кайра иштетүүгө таасир этет?
Материалдардын оюмдуулугуна таасир этүүчү негизги факторлор материалдын түрү, катуулугу жана катуулугу болуп саналат.Материалдык категорияларга металлдык материалдар жана металл эмес материалдар кирет.Жалпысынан алганда, катуулугу канчалык жогору болсо, иштөө жөндөмдүүлүгү ошончолук начар болот, ал эми илешкектүүлүк канчалык жогору болсо, иштөө жөндөмдүүлүгү ошончолук начар болот.Кошумчалар канчалык көп болсо, иштөө жөндөмдүүлүгү ошончолук начарлап, материалдын ичиндеги бөлүкчөлөрдүн катуулугу ошончолук чоңоюп, натыйжада иштөө жөндөмдүүлүгү начарлайт.Жалпы стандарт: көмүртек канчалык көп болсо, ошончолук начар иштетилүүчү, эритме ошончолук жогору, ошончолук начар иштетилүүчү жана металл эмес элементтердин курамы канчалык жогору болсо, ошончолук жакшы болот (бирок жалпысынан металл эмес мазмун материалдар катуу көзөмөлгө алынат).
Кандай материалдар оюп иштетүү үчүн ылайыктуу болуп саналат?
Оюуга ылайыктуу металл эмес материалдарга органикалык айнек, чайыр, жыгач ж.б. кирет. Оюуга жарабаган металл эмес материалдарга табигый мрамор, айнек ж.б. кирет. Оймо жасоо үчүн ылайыктуу металл материалдарга жез, алюминий жана HRC40дан төмөн катуулугу менен жумшак болот кирет. , ал эми оюу үчүн жараксыз металл материалдары өчүрүлгөн болот, ж.б.
Кесүүчү аспаптын өзү иштетүү процессине кандай таасир этет жана ага кандай таасир этет?
Гравюра иштетүүгө таасир этүүчү кесүүчү инструмент факторлоруна шайман материалы, геометриялык параметрлер жана майдалоо технологиясы кирет.Оймо иштетүүдө колдонулган кесүүчү курал материалы порошок эритмеси болгон катуу эритме материал болуп саналат.Материалдын натыйжалуулугун аныктоочу негизги көрсөткүч - порошоктун орточо диаметри.Диаметри канчалык кичине болсо, шайман ошончолук эскирүүгө туруктуу болот жана шаймандын туруктуулугу ошончолук жогору болот.Көбүрөөк NC программалоо билими окуу куралын алуу үчүн WeChat расмий аккаунтуна (NC программалоону үйрөтүү) багытталган.Куралдын курчтугу негизинен кесүүчү күчкө таасирин тийгизет.Курал канчалык курч болсо, кесүүчү күч ошончолук аз, иштетүү ошончолук жылмакай болуп, беттин сапаты ошончолук жогору болот, бирок шаймандын бышыктыгы ошончолук төмөн болот.Ошондуктан, ар кандай материалдарды иштетүүдө ар кандай курчтук тандоо керек.Жумшак жана жабышчаак материалдарды иштетүүдө кесүүчү аспапты курчутуу зарыл.Кайра иштетилген материалдын катуулугу жогору болгондо кесүүчү аспаптын туруктуулугун жогорулатуу үчүн курчтугун азайтуу керек.Бирок бул өтө ачык болушу мүмкүн эмес, антпесе кесүү күчү өтө чоң болуп, иштетүүгө таасир этет.Аспапты майдалоодо негизги фактор - бул так майдалоочу дөңгөлөктүн тор өлчөмү.Жогорку торлуу майдалоочу дөңгөлөк кесүүчү куралдын бышыктыгын эффективдүү жакшыртып, майда кесүүчү кырларды чыгара алат.Тордун чоң өлчөмү менен жылмалоо дөңгөлөктөрү тегиз каптал беттерин түзө алат, бул кесүүнүн бетинин сапатын жакшыртат.
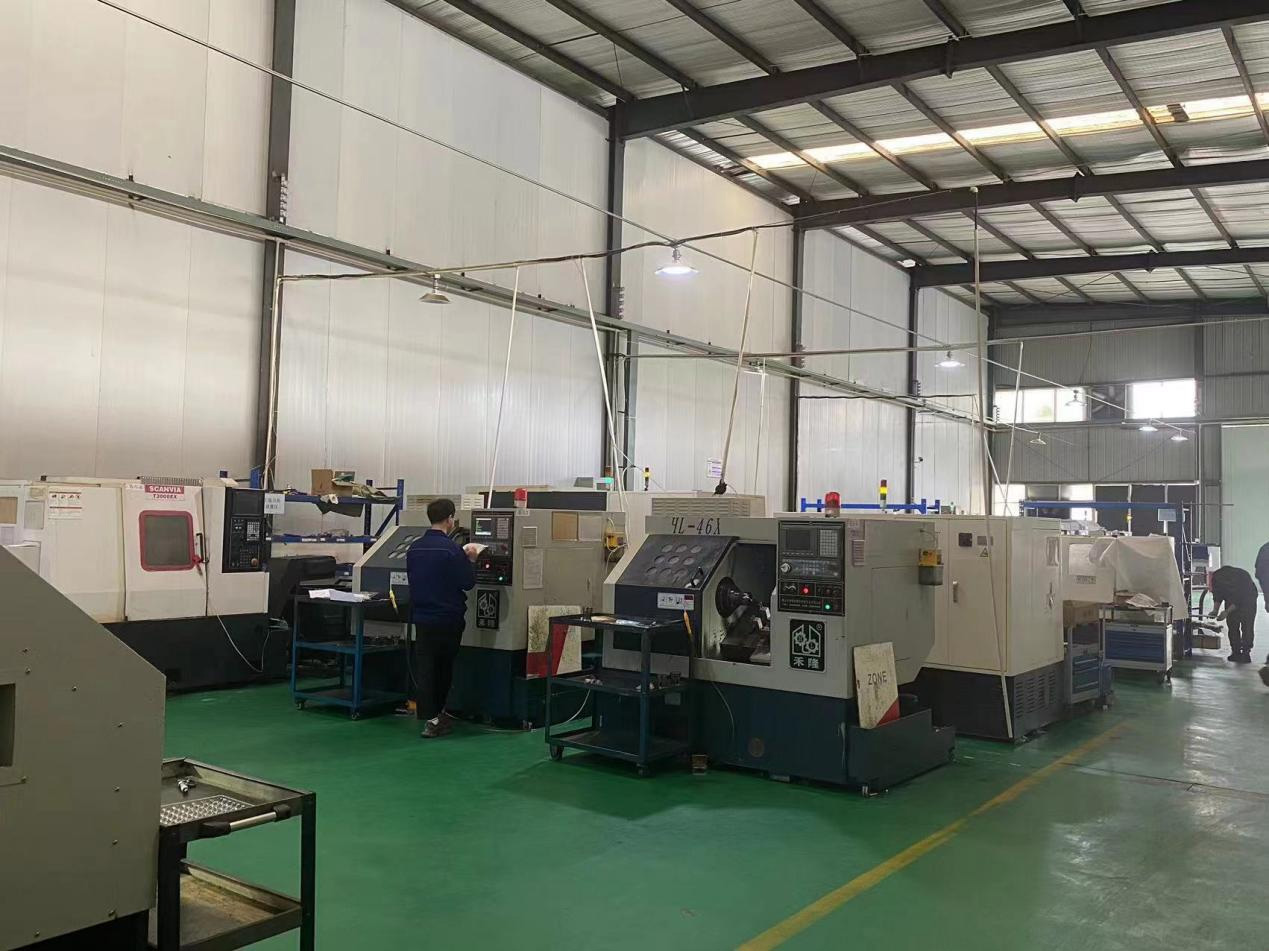
Аспаптын өмүрүнүн формуласы кандай?
Аспаптын иштөө мөөнөтү негизинен болоттон жасалган материалдарды иштетүүдө инструменттердин иштөө мөөнөтүн билдирет.Эмпирикалык формула: (T - инструменттин иштөө мөөнөтү, CT - өмүр параметри, VC - кесүү сызыгынын ылдамдыгы, f - бир айлануудагы кесүү тереңдиги, P - кесүү тереңдиги).Кесүү сызыгынын ылдамдыгы инструменттин иштөө мөөнөтүнө эң чоң таасирин тийгизет.Мындан тышкары, инструменттин радиалдык агымы, шайманды майдалоо сапаты, инструменттин материалы жана жабуусу жана муздаткычы да шаймандын туруктуулугуна таасир этиши мүмкүн.
иштетүү учурунда оюп машина жабдууларды кантип коргоо керек?
1) Аспап орнотуу түзүлүшүн ашыкча май эрозиясынан сактаңыз.
2) Учуучу таштандыларды көзөмөлдөөгө көңүл буруңуз.Учуп бараткан сыныктар станок үчүн чоң коркунуч туудурат.Электр башкаруу шкафына учуу кыска туташууга алып келиши мүмкүн, ал эми жетектөөчү рельске учуу бурамдын жана жетектөөчү рельстин иштөө мөөнөтүн кыскартат.Ошондуктан, кайра иштетүүдө станоктун негизги бөлүктөрүн туура пломбалоо керек.
3) Жарыктыкты жылдырууда лампа капкагын тартпаңыз, анткени ал лампа капкагын оңой бузуп салышы мүмкүн.
4) Өңдөө процессинде көзгө зыян келтирүүчү калдыктардын учуп кетишинен качуу үчүн байкоо жүргүзүү үчүн кесүүчү аймакка жакындабаңыз.Шпинделдин кыймылдаткычы айланып турганда, стендде кандайдыр бир операцияларды жасоого тыюу салынат.
5) Станоктун эшигин ачып жапканда, аны күч менен ачып же жаппаңыз.Тактык менен иштетүү учурунда, эшикти ачуу процессиндеги таасир жана титирөө иштетилген бетинде бычак белгилерин пайда кылышы мүмкүн.
6) Шпинделдин ылдамдыгын берип, андан кийин кайра иштетүүнү баштоо үчүн, антпесе шпинделдин жай башталышына байланыштуу, иштетүү башталганга чейин керектүү ылдамдыкка жете албай, мотордун муунушуна алып келиши мүмкүн.
7) Станоктун кайчылаш устунуна кандайдыр бир инструменттерди же даяр тетиктерди коюуга тыюу салынат.
8) Магниттик соргучтар жана ченегич кармагычтар сыяктуу магниттик шаймандарды электр башкаруу шкафына коюуга катуу тыюу салынат, анткени бул дисплейди бузушу мүмкүн.

Кесүүчү суюктуктун функциясы кандай?
Металл иштетүүдө муздаткыч май кошууга көңүл буруңуз.Муздатуу системасынын милдети кесүүчү жылуулукту жана учкан калдыктарды алып салуу, иштетүү үчүн майлоону камсыз кылуу.Муздаткыч кесүүчү курду жылдырып, кесүүчү аспапка жана моторго берилүүчү жылуулукту азайтат жана алардын иштөө мөөнөтүн жакшыртат.Экинчи кесүүнү болтурбоо үчүн учкан калдыктарды алып салыңыз.Майлоо кесүү күчүн азайтып, иштетүүнү туруктуураак кыла алат.Жезди иштетүүдө майлуу кесүүчү суюктукту колдонуу беттин сапатын жакшыртат.
Инструменттердин кийилиши кандай этаптардан турат?
Кесүүчү аспаптардын эскиришин үч этапка бөлүүгө болот: алгачкы эскирүү, кадимки эскирүү жана курч эскирүү.Баштапкы эскирүү стадиясында инструменттин эскиришинин негизги себеби - инструменттин температурасы төмөн жана оптималдуу кесүү температурасына жетпейт.Бул убакта инструменттин эскириши негизинен абразивдүү эскирүү болуп саналат, ал инструментке көбүрөөк таасирин тийгизет.Көбүрөөк NC программалоо билими WeChat расмий аккаунтуна (санариптик башкарууну программалоону үйрөтүү) багытталган, бул куралдын бузулушуна алып келиши оңой.Бул этап өтө кооптуу жана туура эмес иштетилсе, ал түздөн-түз инструменттин бузулушуна жана бузулушуна алып келиши мүмкүн.Курал баштапкы эскирүү мезгилинен өтүп, кесүү температурасы белгилүү бир мааниге жеткенде, негизги эскирүү диффузиялык эскирүү болуп саналат, ал негизинен жергиликтүү пилингди пайда кылат.Ошентип, эскирүү салыштырмалуу аз жана жай.Эскирүү белгилүү бир деңгээлге жеткенде, курал натыйжасыз болуп, тез эскирүү мезгилине кирет.
Кесүүчү шаймандарды эмне үчүн жана кантип иштетүү керек?
Баштапкы эскирүү стадиясында инструмент бузулууга жакын экенин жогоруда айттык.Сынуу феноменин болтурбоо үчүн биз аспапта иштешибиз керек.Акырындык менен шайманды кесүү температурасын акылга сыярлык температурага чейин жогорулатуу.Эксперименттик текшерүүдөн кийин, салыштыруулар ошол эле иштетүү параметрлерин колдонуу менен жүргүзүлдү.Киргенден кийин инструменттин иштөө мөөнөтү эки эседен ашык көбөйгөнүн көрүүгө болот.
Иштетүү ыкмасы шпинделдин акылга сыярлык ылдамдыгын сактоо менен берүү ылдамдыгын эки эсеге кыскартуу болуп саналат жана иштетүү убактысы болжол менен 5-10 мүнөт.Жумшак материалдарды иштетүүдө кичине мааниге ээ, ал эми катуу металлдарды иштетүүдө чоң мааниге ээ.
Куралдын катуу эскиришин кантип аныктоого болот?
Куралдын катуу эскирүүсүн аныктоо ыкмасы:
1) иштетүү үнүн угуп, катаал чалуу;
2) Шпинделдин үнүн угуп, шпиндельди кармап калуу байкалаарлык көрүнүш;
3) иштетүүдө термелүү күчөп, станоктун шпиндельинде айкын титирөө бар экенин сезүү;
4) иштетүү эффектинин негизинде, иштетилген ылдыйкы бычактын үлгүсү жакшы же жаман болушу мүмкүн (эгер башында ушундай болсо, бул кесүү тереңдиги өтө терең экенин көрсөтүп турат).
Бычакты качан алмаштыруу керек?
Биз аспапты куралдын иштөө мөөнөтүнүн 2/3 бөлүгүнө алмаштырышыбыз керек.Мисалы, эгерде курал 60 мүнөттүн ичинде катуу эскирсе, кийинки иштетүү 40 мүнөттүн ичинде инструментти алмаштырууну баштап, куралды үзгүлтүксүз алмаштыруу адатын өнүктүрүү керек.
Катуу эскирген инструменттерди кайра иштетүүгө болобу?
Курал катуу эскиргенден кийин кесүү күчү нормадан үч эсеге чейин көбөйүшү мүмкүн.Кесүүчү күч шпиндель электродунун иштөө мөөнөтүнө олуттуу таасирин тийгизет, ал эми шпиндель кыймылдаткычынын иштөө мөөнөтү менен күчтүн ортосундагы байланыш үчүнчү күчкө тескери пропорционалдуу.Мисалы, кесүү күчү үч эсеге көбөйгөндө 10 мүнөттүк иштетүү кадимки шарттарда шпиндельди 10 * 33=270 мүнөттө колдонууга барабар.
Орой иштетүүдө аспаптын узартуу узундугун кантип аныктоого болот?
Куралдын узартуу узундугу канчалык кыска болсо, ошончолук жакшы.Бирок, иш жүзүндө иштетүүдө, эгерде ал өтө кыска болсо, инструменттин узундугун бат-баттан тууралоо керек, бул иштетүүнүн натыйжалуулугуна чоң таасирин тийгизет.Ошентип, кесүүчү аспаптын узартуу узундугун иш жүзүндө иштетүүдө кантип көзөмөлдөө керек?Принцип төмөнкүчө: φ Диаметри 3 болгон шайман тилкесин 5мм узартуу менен кадимкидей иштетүүгө болот.φ 4-диаметрдик кескич тилкесин 7мм узартуу менен кадимкидей иштетүүгө болот.φ 6-диаметрдик кескич тилкесин 10мм узартуу менен кадимкидей иштетүүгө болот.Кесүүдө бул баалуулуктардан төмөн жетүүгө аракет кылыңыз.Эгерде үстүнкү аспаптын узундугу жогорудагы мааниден чоңураак болсо, инструмент эскиргенде аны иштетүү тереңдигине чейин көзөмөлдөөгө аракет кылыңыз.Муну түшүнүү бир аз кыйын жана көбүрөөк машыгууну талап кылат.
кайра иштетүү учурунда күтүлбөгөн жерден курал сынган кантип чечүү керек?
1) иштетүүнү токтотуңуз жана иштетүүнүн учурдагы сериялык номерин көрүңүз.
2) Кесүүчү жерде сынган бычактын бар же жок экенин текшериңиз, эгерде бар болсо, аны алып салыңыз.
3) Эң негизгиси сынган куралдын себебин талдаңыз.Эмне үчүн курал сынып калды?Биз жогоруда айтылган кайра иштетүүгө таасир этүүчү ар кандай факторлорду талдап чыгышыбыз керек.Ал эми аспаптын сынганынын себеби, аспапка болгон күч бир заматта күчөйт.Же бул жол маселеси, же ашыкча шайман титиреп жатат, же материалда катуу блоктор бар, же шпиндель моторунун ылдамдыгы туура эмес.
4) Талдоодон кийин, кайра иштетүү үчүн куралды алмаштыруу.Эгерде жол өзгөртүлбөсө, иштетүү баштапкы сандан бир сан алдыда жүргүзүлүшү керек.Бул учурда тоюттун ылдамдыгын азайтууга кецул буруу керек.Себеби, аспаптын үзүлүшүндө катуулануу катуу болот, ошондой эле инструментти иштетүү керек.
Орой иштетүү жакшы эмес болгондо иштетүү параметрлерин кантип тууралоо керек?
Аспаптын иштөө мөөнөтүн акылга сыярлык негизги ок ылдамдыгы менен камсыз кылуу мүмкүн болбосо, параметрлерди тууралоодо, адегенде кесүү тереңдигин тууралаңыз, андан кийин берүү ылдамдыгын тууралаңыз, андан кийин каптал берүү ылдамдыгын дагы бир жолу тууралаңыз.(Эскертүү: Кесүү тереңдигин тууралоодо да чектөөлөр бар. Кесүү тереңдиги өтө аз жана катмарлар өтө көп болсо, теориялык кесүү эффективдүүлүгү жогору болушу мүмкүн. Бирок, иш жүзүндө иштетүү натыйжалуулугуна башка факторлор таасир этет, бул өтө төмөн иштетүүгө алып келет. Бул учурда кесүүчү аспапты кайра иштетүү үчүн кичинесине алмаштыруу керек, бирок иштетүү эффективдүүлүгү жогору. Жалпысынан алганда, минималдуу кесүү тереңдиги 0,1 ммден кем болбошу керек.).
Посттун убактысы: 13-апрель-2023