CNC-kaiverruskoneet ovat taitavia tarkkuuskoneistuksessa pienillä työkaluilla, ja niillä on kyky jyrsimiseen, hiontaan, poraamiseen ja nopeaan kierteitykseen.Niitä käytetään laajasti eri aloilla, kuten 3C-teollisuudessa, muottiteollisuudessa ja lääketeollisuudessa.Tämä artikkeli kerää yleisiä kysymyksiä CNC-kaiverruskäsittelystä.
Mitkä ovat tärkeimmät erot CNC-kaiverruksen ja CNC-jyrsinnän välillä?
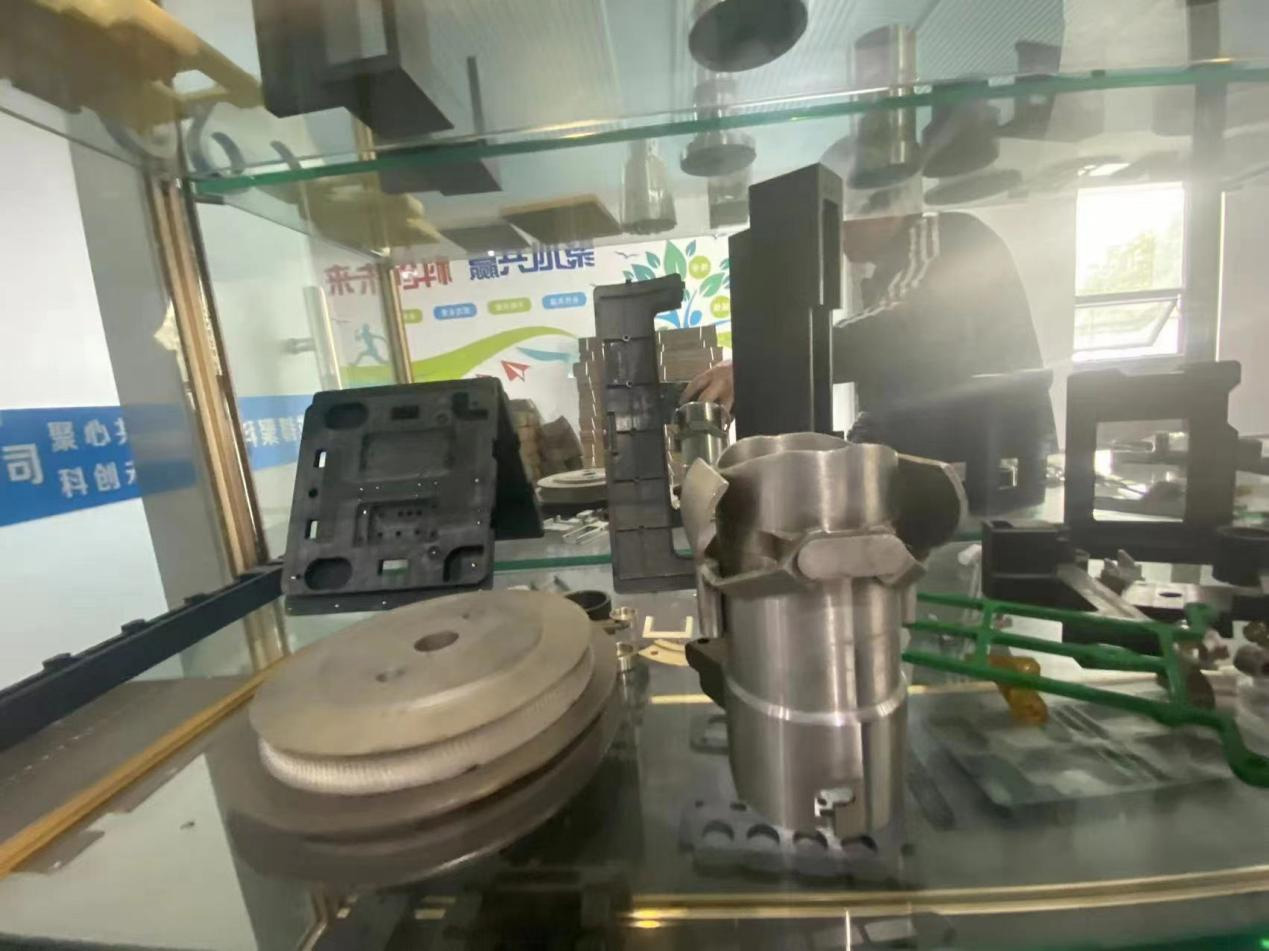
Sekä CNC-kaiverrus- että CNC-jyrsintäprosesseissa käytetään jyrsintäperiaatteita.Suurin ero on käytetyssä työkalun halkaisijassa: CNC-jyrsinnässä yleisesti käytetty työkalun halkaisija on 6–40 millimetriä, kun taas CNC-kaiverruskäsittelyn työkalun halkaisija vaihtelee välillä 0,2–3 millimetriä.
Voidaanko CNC-jyrsintä käyttää vain karkeaan koneistukseen, kun taas CNC-kaiverrusta voidaan käyttää vain tarkkuuskoneistukseen?
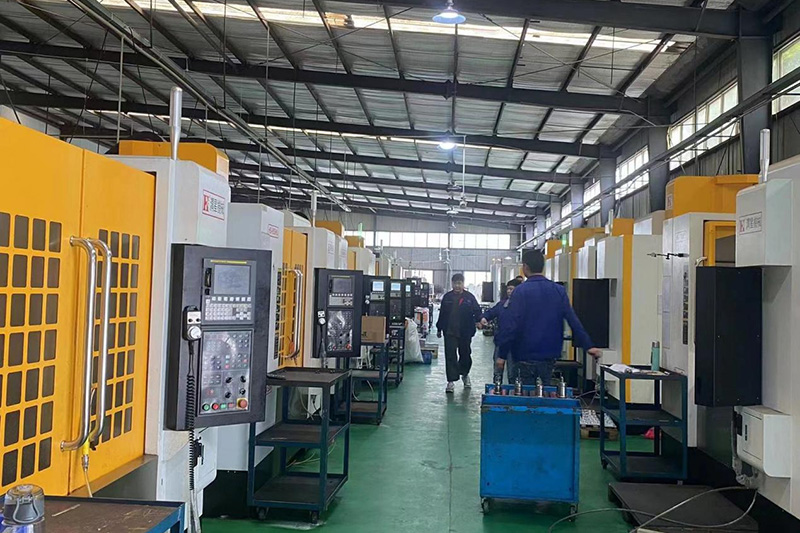
Ennen kuin vastaat tähän kysymykseen, on ensin ymmärrettävä prosessin käsite.Karkean koneistuksen prosessointivolyymi on suuri, kun taas tarkkuuskoneistuksen käsittelymäärä on pieni, joten jotkut ihmiset pitävät tavallisesti karkeaa koneistusta "raskasleikkauksena" ja tarkkuustyöstöä "kevytleikkauksena".Itse asiassa karkea koneistus, puolitarkkuuskoneistus ja tarkkuuskoneistus ovat prosessikonsepteja, jotka edustavat eri käsittelyvaiheita.Joten tarkka vastaus tähän kysymykseen on, että CNC-jyrsintä voi tehdä raskaan tai kevyen leikkaamisen, kun taas CNC-kaiverrus voi tehdä vain kevyen leikkaamisen.
Voidaanko CNC-kaiverrusprosessia käyttää teräsmateriaalien karkeaan työstöön?
Sen arvioiminen, pystyykö CNC-kaiverrus käsittelemään tiettyä materiaalia, riippuu pääasiassa siitä, kuinka suurta työkalua voidaan käyttää.CNC-kaiverrusprosessoinnissa käytettävät leikkaustyökalut määräävät sen suurimman leikkauskapasiteetin.Jos muotin muoto sallii halkaisijaltaan yli 6 millimetrin työkalujen käytön, on erittäin suositeltavaa käyttää ensin CNC-jyrsintä ja sitten käyttää veistämistä jäljellä olevan materiaalin poistamiseen.
Voiko nopeutta lisäävän pään lisääminen CNC-työstökeskuksen karaan täydentää kaiverruskäsittelyn?
Ei voida suorittaa loppuun.Tämä tuote ilmestyi näyttelyyn kaksi vuotta sitten, mutta kaiverrusprosessia ei voitu suorittaa loppuun.Pääsyynä on se, että CNC-työstökeskusten suunnittelussa huomioidaan oma työkaluvalikoima ja kokonaisrakenne ei sovellu kaiverruskäsittelyyn.Pääsyy tähän virheelliseen ajatukseen on se, että he luulivat nopean sähkökaran kaiverruskoneen ainoaksi ominaisuudeksi.
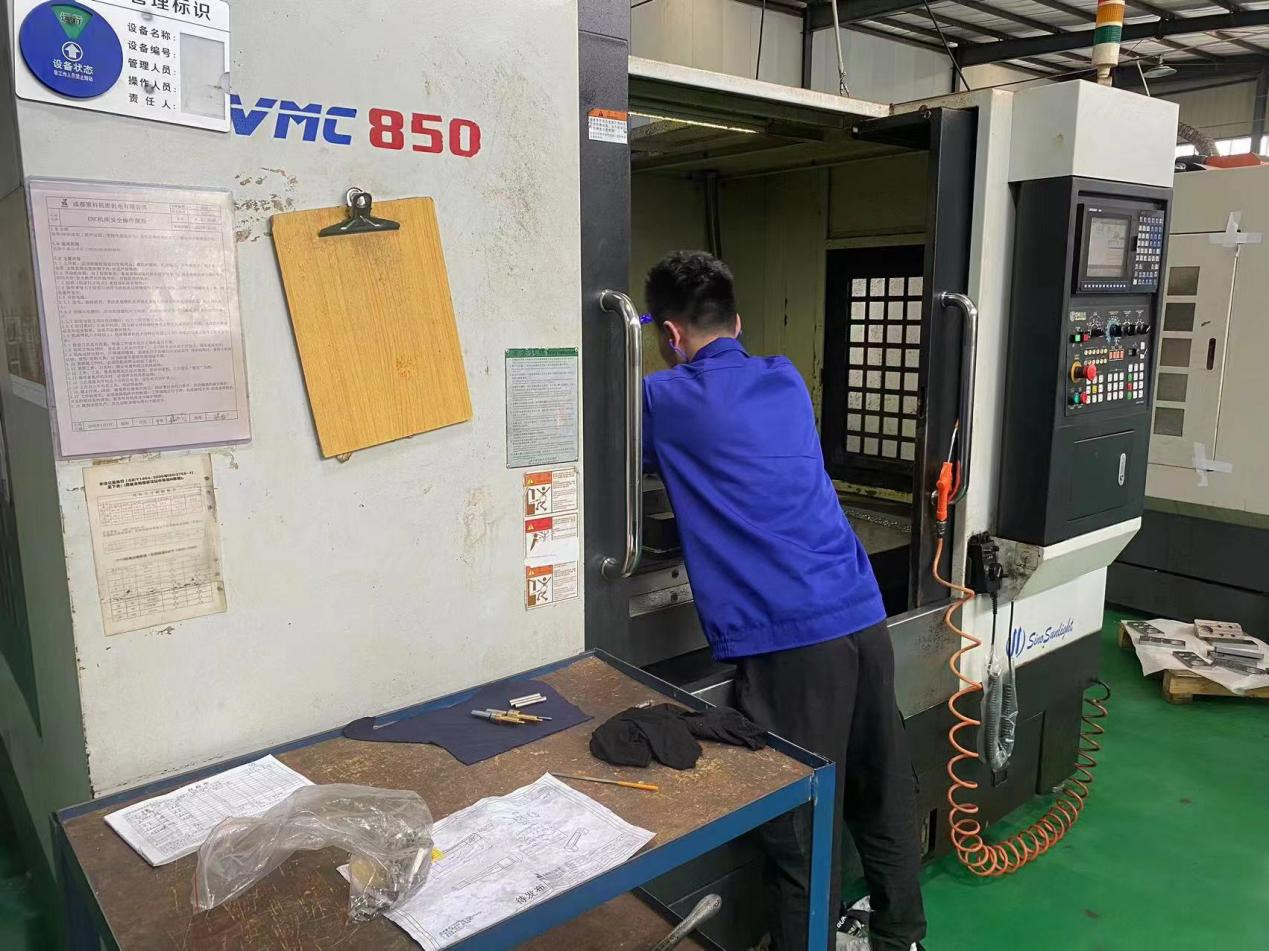
Mitkä ovat tärkeimmät tekijät, jotka vaikuttavat kaiverruksen käsittelyyn?
Mekaaninen käsittely on suhteellisen monimutkainen prosessi, ja siihen vaikuttavat monet tekijät, mukaan lukien lähinnä seuraavat: työstökoneiden ominaisuudet, leikkaustyökalut, ohjausjärjestelmät, materiaalin ominaisuudet, työstötekniikka, apulaitteet ja ympäristö.
Mitä vaatimuksia ohjausjärjestelmälle on CNC-kaiverruskäsittelyssä?
CNC-kaiverruskäsittely on ensisijaisesti jyrsintäkäsittelyä, joten ohjausjärjestelmällä on oltava kyky ohjata jyrsintäkäsittelyä.Pienen työkalun koneistuksessa on oltava eteenpäinsyöttötoiminto, joka hidastaa rataa etukäteen ja vähentää työkalun rikkoutumistiheyttä.Samalla on tarpeen lisätä leikkausnopeutta suhteellisen tasaisissa polun osissa kaiverruskäsittelyn tehokkuuden parantamiseksi.
Mitkä materiaalien ominaisuudet vaikuttavat käsittelyyn?
Tärkeimmät materiaalien veistosominaisuuksiin vaikuttavat tekijät ovat materiaalityyppi, kovuus ja sitkeys.Materiaaliluokat sisältävät metalliset materiaalit ja ei-metalliset materiaalit.Kaiken kaikkiaan mitä suurempi kovuus, sitä huonompi työstettävyys, kun taas mitä korkeampi viskositeetti, sitä huonompi työstettävyys.Mitä enemmän epäpuhtauksia, sitä huonompi työstettävyys ja sitä suurempi on materiaalin sisällä olevien hiukkasten kovuus, mikä heikentää työstettävyyttä.Yleinen standardi on: mitä korkeampi hiilipitoisuus, sitä huonompi työstettävyys, korkeampi seospitoisuus, sitä huonompi työstettävyys, ja mitä suurempi ei-metallisten elementtien pitoisuus, sitä parempi työstettävyys (mutta ei-metallipitoisuus yleensä materiaalia valvotaan tiukasti).
Mitkä materiaalit sopivat kaiverruskäsittelyyn?
Kaiverrukseen soveltuvia ei-metallisia materiaaleja ovat orgaaninen lasi, hartsi, puu jne. Ei-metallisia materiaaleja, jotka eivät sovellu kaiverrukseen, ovat luonnonmarmori, lasi jne. Sopivia metallimateriaaleja kaiverrukseen ovat kupari, alumiini ja pehmeä teräs, jonka kovuus on alle HRC40 , kun taas veistokseen soveltumattomia metallimateriaaleja ovat karkaistu teräs jne.
Mikä on itse leikkaustyökalun vaikutus koneistusprosessiin ja miten se vaikuttaa siihen?
Kaiverruskäsittelyyn vaikuttavia leikkaustyökalutekijöitä ovat työkalumateriaali, geometriset parametrit ja hiontatekniikka.Kaiverruskäsittelyssä käytetty leikkaustyökalumateriaali on kovaseosmateriaalia, joka on jauheseos.Tärkein suoritusindikaattori, joka määrittää materiaalin suorituskyvyn, on jauheen keskimääräinen halkaisija.Mitä pienempi halkaisija on, sitä kulutusta kestävämpi työkalu on ja sitä parempi työkalun kestävyys.Lisää NC-ohjelmointitietoa keskittyy WeChatin viralliseen tiliin (NC-ohjelmoinnin opetus) saadaksesi opetusohjelman.Työkalun terävyys vaikuttaa pääasiassa leikkausvoimaan.Mitä terävämpi työkalu, sitä pienempi leikkausvoima, sitä tasaisempi käsittely ja korkeampi pinnan laatu, mutta sitä huonompi työkalun kestävyys.Siksi eri materiaalien käsittelyssä tulee valita eri terävyys.Pehmeitä ja tahmeita materiaaleja käsiteltäessä on tarpeen teroittaa leikkuutyökalu.Kun käsitellyn materiaalin kovuus on korkea, terävyyttä tulee vähentää leikkuutyökalun kestävyyden parantamiseksi.Mutta se ei voi olla liian tylsä, muuten leikkausvoima on liian suuri ja vaikuttaa koneistukseen.Keskeinen tekijä työkalun hionnassa on tarkkuushiomalaikan silmäkoko.Suuriverkkoinen hiomalaikka voi tuottaa hienompia leikkaussärmiä, mikä parantaa tehokkaasti leikkuutyökalun kestävyyttä.Suuren silmäkoon omaavat hiomalaikat voivat tuottaa sileämpiä kylkipintoja, mikä voi parantaa leikkauspinnan laatua.
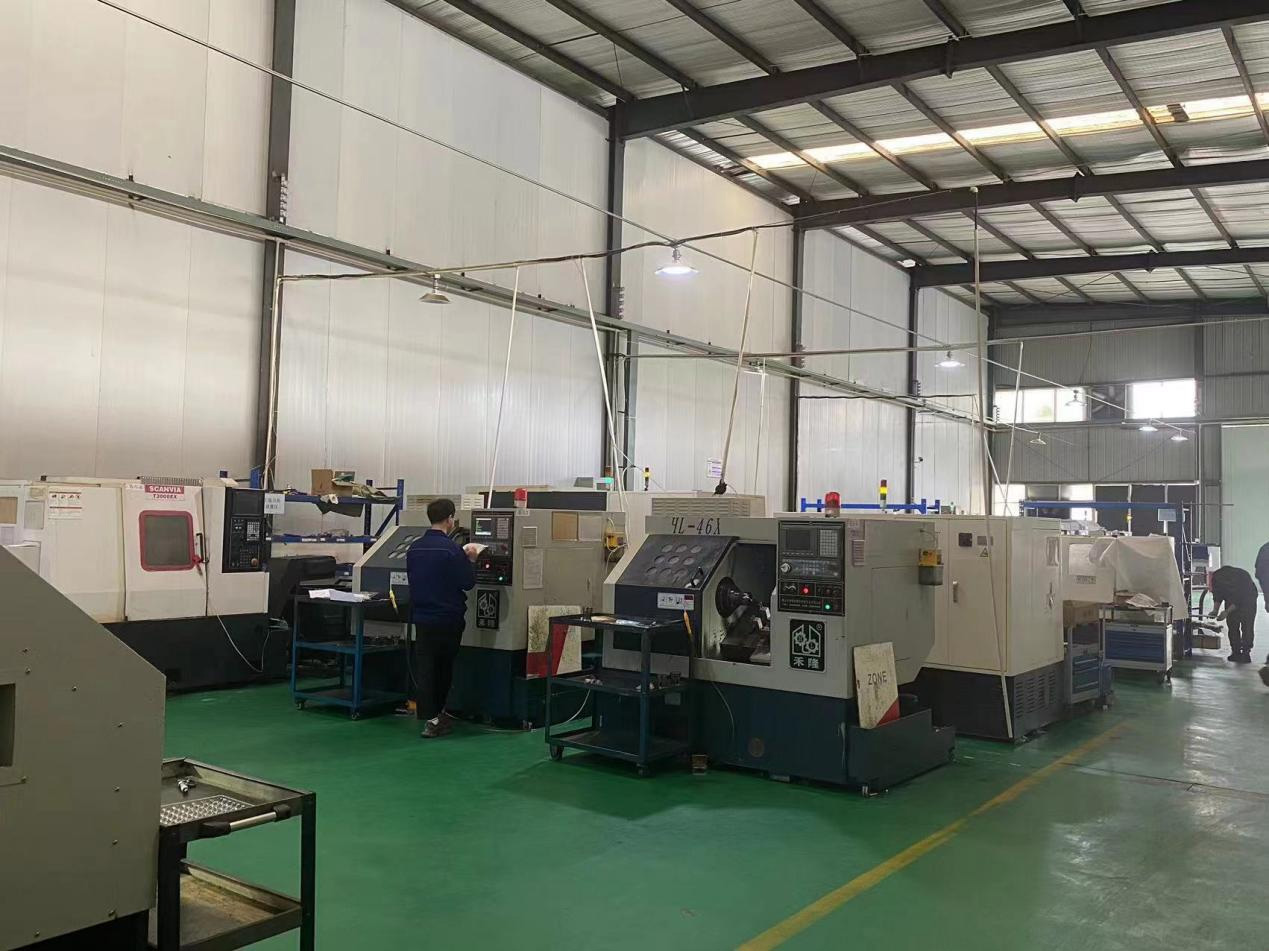
Mikä on työkalun käyttöiän kaava?
Työkalun käyttöikä viittaa pääasiassa työkalun käyttöikään teräsmateriaalien käsittelyn aikana.Empiirinen kaava on: (T on työkalun käyttöikä, CT on käyttöikäparametri, VC on leikkauslinjan nopeus, f on leikkaussyvyys kierrosta kohti ja P on leikkaussyvyys).Leikkuulinjan nopeudella on suurin vaikutus työkalun käyttöikään.Lisäksi työkalun säteittäinen valuminen, työkalun hiontalaatu, työkalun materiaali ja pinnoite sekä jäähdytysneste voivat vaikuttaa työkalun kestävyyteen.
Kuinka suojata kaiverruskoneen laitteita käsittelyn aikana?
1) Suojaa työkalun säätölaitetta liialliselta öljyeroosiolta.
2) Kiinnitä huomiota lentävien roskien hallintaan.Lentävät roskat muodostavat suuren uhan työstökoneelle.Ohjauskaappiin lentäminen voi aiheuttaa oikosulun ja ohjauskiskoon lentäminen voi lyhentää ruuvin ja ohjauskiskon käyttöikää.Siksi työstön aikana työstökoneen pääosat tulee sulkea kunnolla.
3) Kun siirrät valaisinta, älä vedä lampun kantta, koska se voi vahingoittaa lampun suojusta helposti.
4) Työstön aikana ei saa lähestyä leikkausaluetta tarkkailua varten, jotta vältytään lentävältä roskilta, jotka voivat vahingoittaa silmiä.Karan moottorin pyöriessä minkään toiminnan suorittaminen työpöydällä on kielletty.
5) Kun avaat ja suljet koneen luukkua, älä avaa tai sulje sitä väkisin.Tarkkuustyöstössä oven avaamisen aikana tapahtuva isku ja tärinä voivat aiheuttaa veitsen jälkiä työstettävälle pinnalle.
6) Karan nopeuden antamiseksi ja sen jälkeen prosessoinnin aloittamiseksi, muuten karan hitaan käynnistymisen vuoksi haluttua nopeutta ei ehkä saavuteta ennen käsittelyn aloittamista, mikä aiheuttaa moottorin tukehtumisen.
7) On kiellettyä asettaa työkaluja tai työkappaleita koneen poikkipalkkiin.
8) Magneettisten työkalujen, kuten magneettisten imukuppien ja mittakellon pidikkeiden asettaminen sähköiseen ohjauskaappiin on ehdottomasti kielletty, koska tämä voi vahingoittaa näyttöä.

Mikä on leikkausnesteen tehtävä?
Kiinnitä huomiota jäähdytysöljyn lisäämiseen metallin käsittelyn aikana.Jäähdytysjärjestelmän tehtävänä on poistaa leikkauslämpö ja lentävät roskat, jotka tarjoavat voitelua koneistukseen.Jäähdytysneste liikuttaa leikkuuhihnaa vähentäen leikkaustyökaluun ja moottoriin siirtyvää lämpöä ja pidentäen niiden käyttöikää.Poista lentävät roskat välttääksesi toissijaisen leikkauksen.Voitelu voi vähentää leikkausvoimaa ja tehdä työstöstä vakaampaa.Kuparin käsittelyssä öljymäisen leikkausnesteen käyttö voi parantaa pinnan laatua.
Mitkä ovat työkalujen kulumisen vaiheet?
Leikkuutyökalujen kuluminen voidaan jakaa kolmeen vaiheeseen: alkukuluminen, normaali kuluminen ja terävä kuluminen.Alkuvaiheessa työkalun kulumisen pääasiallinen syy on se, että työkalun lämpötila on alhainen eikä saavuta optimaalista leikkauslämpötilaa.Tällä hetkellä työkalun kuluminen on pääasiassa hankaavaa kulumista, jolla on suurempi vaikutus työkaluun.Lisää NC-ohjelmointiosaaminen keskittyy WeChatin viralliseen tiliin (digitaalisen ohjauksen ohjelmoinnin opetus) saadaksesi opetusohjelman, joka on helppo aiheuttaa työkalun rikkoutumista.Tämä vaihe on erittäin vaarallinen, ja jos sitä ei käsitellä oikein, se voi suoraan johtaa työkalun rikkoutumiseen ja epäonnistumiseen.Kun työkalu ylittää alkukulumisajan ja leikkauslämpötila saavuttaa tietyn arvon, pääasiallinen kuluminen on diffuusiokulumista, joka aiheuttaa pääasiassa paikallista kuoriutumista.Joten kuluminen on suhteellisen pientä ja hidasta.Kun kuluminen saavuttaa tietyn tason, työkalu muuttuu tehottomaksi ja siirtyy nopeaan kulumisjaksoon.
Miksi ja miten leikkuutyökalut pitää ajaa sisään?
Mainitsimme edellä, että alkukulumisvaiheessa työkalu on alttiina rikkoutumaan.Rikkoutumisilmiön välttämiseksi meidän on käytettävä työkalua.Nosta työkalun leikkauslämpötilaa asteittain kohtuulliseen lämpötilaan.Kokeellisen tarkastuksen jälkeen vertailut tehtiin samoilla prosessointiparametreilla.Voidaan nähdä, että sisäänajon jälkeen työkalun käyttöikä on pidentynyt yli kaksinkertaiseksi.
Sisäänajomenetelmänä on puolittaa syöttönopeus ja säilyttää karan nopeus kohtuullisena ja käsittelyaika on noin 5-10 minuuttia.Pehmeitä materiaaleja käsiteltäessä ota pieni arvo ja kovia metalleja käsiteltäessä suuri arvo.
Kuinka määrittää työkalujen vakava kuluminen?
Menetelmä työkalun vakavan kulumisen määrittämiseksi on:
1) Kuuntele käsittelyääntä ja soita kova puhelu;
2) Karan ääntä kuunnellessa on havaittavissa karan jarrutusilmiö;
3) Tunne, että tärinä lisääntyy käsittelyn aikana ja työstökoneen karassa on ilmeistä tärinää;
4) Prosessointivaikutuksen perusteella käsitelty pohjaterän kuvio voi olla hyvä tai huono (jos näin on alussa, se osoittaa, että leikkaussyvyys on liian syvä).
Milloin minun pitäisi vaihtaa veitsi?
Meidän tulisi vaihtaa työkalu noin 2/3 työkalun käyttöiästä.Jos työkalu esimerkiksi kuluu voimakkaasti 60 minuutin kuluessa, seuraavan käsittelyn tulee aloittaa työkalun vaihto 40 minuutin kuluessa ja kehittää tapa vaihtaa työkalu säännöllisesti.
Voidaanko pahoin kuluneita työkaluja työstää edelleen?
Kovan työkalun kulumisen jälkeen leikkausvoima voi kasvaa kolminkertaiseksi.Leikkausvoimalla on merkittävä vaikutus karaelektrodin käyttöikään, ja karamoottorin käyttöiän ja voiman välinen suhde on kääntäen verrannollinen kolmanteen tehoon.Esimerkiksi kun leikkausvoima kasvaa kolme kertaa, 10 minuutin käsittely vastaa karan käyttöä 10 * 33=270 minuuttia normaaleissa olosuhteissa.
Kuinka määrittää työkalun jatkepituus karkean työstön aikana?
Mitä lyhyempi työkalun pidennyspituus, sitä parempi.Kuitenkin varsinaisessa koneistuksessa, jos se on liian lyhyt, työkalun pituutta on säädettävä usein, mikä voi vaikuttaa suuresti koneistuksen tehokkuuteen.Miten leikkuutyökalun pituutta sitten pitäisi ohjata varsinaisessa koneistuksessa?Periaate on seuraava: φ Työkalupalkki, jonka halkaisija on 3, voidaan työstää normaalisti pidentämällä 5 mm.φ 4-halkaisijainen teräpalkki voidaan työstää normaalisti pidentämällä 7 mm.φ 6-halkaisijainen teräpalkki voidaan työstää normaalisti pidentämällä 10 mm.Yritä päästä näiden arvojen alapuolelle leikkaaessasi.Jos ylätyökalun pituus on suurempi kuin yllä oleva arvo, yritä ohjata sitä työstösyvyyteen, kun työkalu kuluu.Tämä on hieman vaikea ymmärtää ja vaatii lisää koulutusta.
Kuinka käsitellä äkillistä työkalun rikkoutumista käsittelyn aikana?
1) Lopeta koneistus ja katso koneistuksen nykyinen sarjanumero.
2) Tarkista, onko leikkauskohdassa katkennut terä, ja jos on, poista se.
3) Analysoi rikkinäisen työkalun syy, mikä on tärkein.Miksi työkalu meni rikki?Meidän on analysoitava edellä mainituista käsittelyyn vaikuttavista eri tekijöistä.Mutta syynä rikkinäiseen työkaluun on se, että työkaluun kohdistuva voima kasvaa yhtäkkiä.Joko se on rataongelma, työkalu tärisee liikaa, materiaalissa on kovia lohkoja tai karamoottorin nopeus on väärä.
4) Vaihda työkalu analyysin jälkeen käsittelyä varten.Jos polkua ei ole muutettu, koneistus tulee suorittaa yksi numero alkuperäistä numeroa edellä.Tällä hetkellä on tarpeen kiinnittää huomiota syöttönopeuden vähentämiseen.Tämä johtuu siitä, että karkaisu työkalun murtokohdassa on voimakasta ja työkalun sisäänajo on myös tarpeen.
Kuinka säätää käsittelyparametreja, kun karkea koneistus ei ole hyvä?
Jos työkalun käyttöikää ei voida taata kohtuullisella pääakselin nopeudella, säädä parametreja säädettäessä ensin leikkaussyvyys, sitten syöttönopeus ja sitten sivusyöttönopeus uudelleen.(Huom: Leikkaussyvyyden säätämisellä on myös rajoituksia. Jos leikkaussyvyys on liian pieni ja kerroksia on liikaa, teoreettinen leikkaustehokkuus voi olla korkea. Todelliseen käsittelytehokkuuteen vaikuttavat kuitenkin muut tekijät, mikä johtaa liian alhaiseen käsittelyyn tehokkuus. Tässä vaiheessa leikkaustyökalu on tarpeen vaihtaa pienempään käsittelyä varten, mutta työstötehokkuus on korkeampi. Yleisesti ottaen pienin leikkaussyvyys ei voi olla pienempi kuin 0,1 mm.).
Postitusaika: 13.4.2023