Maszyny grawerujące CNC są wykwalifikowane w precyzyjnej obróbce małymi narzędziami i posiadają zdolność frezowania, szlifowania, wiercenia i gwintowania z dużą prędkością.Są szeroko stosowane w różnych dziedzinach, takich jak przemysł 3C, przemysł form i przemysł medyczny.W tym artykule zebrano często zadawane pytania dotyczące obróbki grawerowania CNC.
Jakie są główne różnice pomiędzy grawerowaniem CNC a frezowaniem CNC?
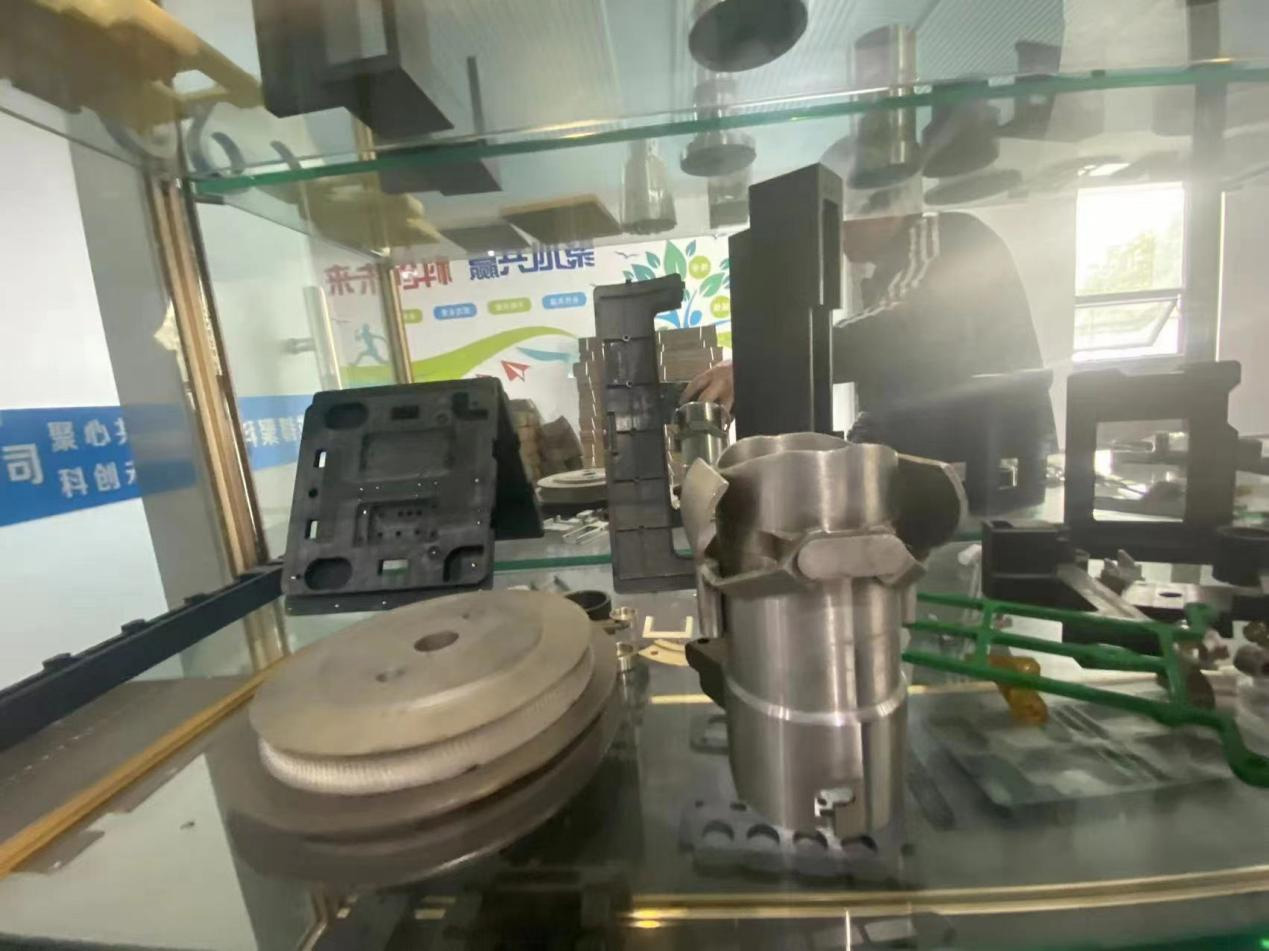
Zarówno procesy grawerowania CNC, jak i frezowania CNC wykorzystują zasady frezowania.Główna różnica polega na zastosowanej średnicy narzędzia, przy czym powszechnie stosowany zakres średnic narzędzi do frezowania CNC wynosi od 6 do 40 milimetrów, natomiast średnica narzędzia do obróbki grawerowania CNC waha się od 0,2 do 3 milimetrów.
Czy frezowanie CNC można stosować tylko do obróbki zgrubnej, a grawerowanie CNC można stosować tylko do obróbki precyzyjnej?
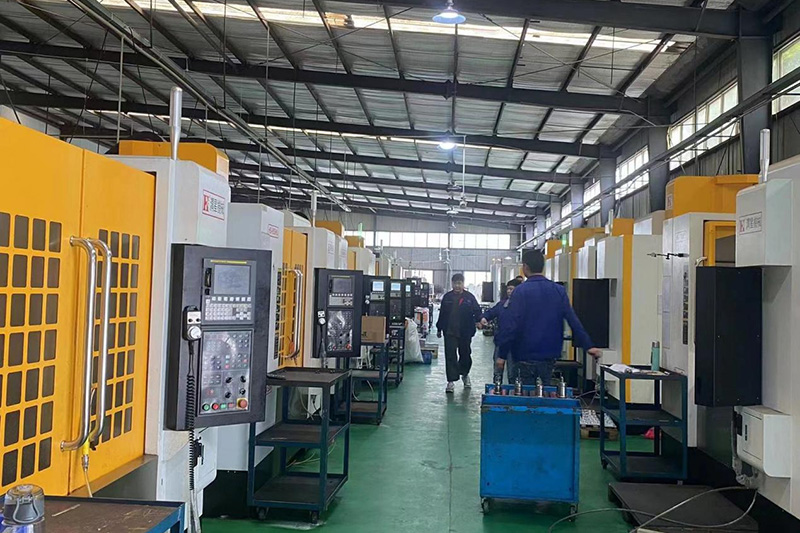
Zanim odpowiemy na to pytanie, najpierw zrozummy koncepcję procesu.Wielkość obróbki zgrubnej jest duża, podczas gdy wielkość obróbki precyzyjnej jest niewielka, dlatego niektórzy ludzie zwykle uważają obróbkę zgrubną za „ciężką obróbkę”, a obróbkę precyzyjną za „lekkie cięcie”.W rzeczywistości obróbka zgrubna, obróbka półprecyzyjna i obróbka precyzyjna to koncepcje procesów reprezentujące różne etapy przetwarzania.Zatem dokładna odpowiedź na to pytanie jest taka, że frezowanie CNC może wykonywać ciężkie lub lekkie cięcie, podczas gdy grawerowanie CNC może wykonywać tylko lekkie cięcie.
Czy proces grawerowania CNC można zastosować do obróbki zgrubnej materiałów stalowych?
Ocena, czy grawerowanie CNC może obrobić dany materiał, zależy głównie od tego, jak duże można zastosować narzędzie.Narzędzia skrawające stosowane w obróbce grawerowania CNC decydują o jego maksymalnej wydajności cięcia.Jeżeli kształt formy pozwala na zastosowanie narzędzi o średnicy przekraczającej 6 milimetrów, zdecydowanie zaleca się w pierwszej kolejności zastosować frezowanie CNC, a następnie zastosować rzeźbienie w celu usunięcia pozostałego materiału.
Czy dodanie głowicy zwiększającej prędkość do wrzeciona centrum obróbczego CNC może zakończyć proces grawerowania?
Nie można ukończyć.Produkt ten pojawił się na wystawie dwa lata temu, lecz nie udało się dokończyć procesu rzeźbienia.Głównym powodem jest to, że konstrukcja centrów obróbczych CNC uwzględnia ich własny zakres narzędzi, a ogólna konstrukcja nie nadaje się do obróbki grawerskiej.Głównym powodem tego błędnego poglądu jest to, że szybkobieżne wrzeciono elektryczne zostało uznane za jedyną cechę maszyny grawerującej.
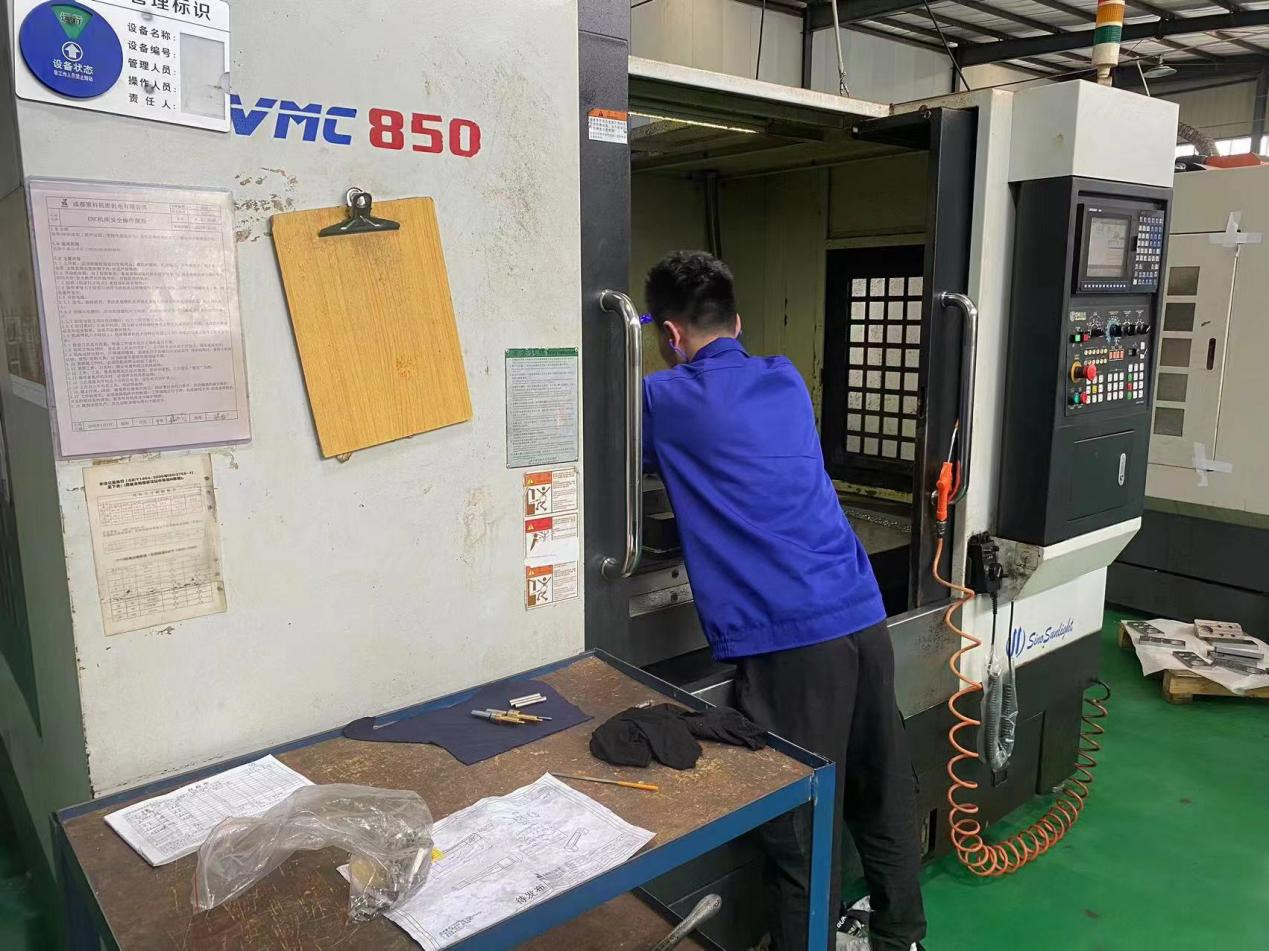
Jakie są główne czynniki wpływające na obróbkę rzeźbienia?
Obróbka mechaniczna jest procesem stosunkowo złożonym i ma na nią wpływ wiele czynników, do których zaliczają się głównie: charakterystyka obrabiarki, narzędzia skrawające, systemy sterowania, charakterystyka materiału, technologia przetwarzania, osprzęt pomocniczy i otaczające środowisko.
Jakie są wymagania dla układu sterowania w obróbce grawerowania CNC?
Obróbka grawerska CNC to przede wszystkim obróbka frezarska, dlatego układ sterowania musi mieć możliwość sterowania obróbką frezarską.W przypadku obróbki małych narzędzi należy zapewnić funkcję wyprzedzającą, aby z wyprzedzeniem spowolnić ścieżkę i zmniejszyć częstotliwość pękania narzędzia.Jednocześnie konieczne jest zwiększenie prędkości skrawania w stosunkowo gładkich odcinkach ścieżki, aby poprawić efektywność obróbki grawerskiej.
Jakie cechy materiałów będą miały wpływ na przetwarzanie?
Głównymi czynnikami wpływającymi na wydajność rzeźbienia materiałów są rodzaj materiału, twardość i wytrzymałość.Kategorie materiałów obejmują materiały metaliczne i materiały niemetalowe.Ogólnie rzecz biorąc, im wyższa twardość, tym gorsza urabialność, natomiast im wyższa lepkość, tym gorsza urabialność.Im więcej zanieczyszczeń, tym gorsza urabialność i większa twardość cząstek wewnątrz materiału, co skutkuje gorszą urabialnością.Ogólna norma jest następująca: im wyższa zawartość węgla, tym gorsza urabialność, im wyższa zawartość stopu, tym gorsza urabialność i im wyższa zawartość pierwiastków niemetalicznych, tym lepsza urabialność (ale ogólnie zawartość niemetali materiały są ściśle kontrolowane).
Jakie materiały nadają się do obróbki rzeźbiarskiej?
Materiały niemetalowe odpowiednie do rzeźbienia obejmują szkło organiczne, żywicę, drewno itp. Materiały niemetalowe nienadające się do rzeźbienia obejmują naturalny marmur, szkło itp. Odpowiednie materiały metalowe do rzeźbienia obejmują miedź, aluminium i miękką stal o twardości mniejszej niż HRC40 , podczas gdy nieodpowiednie materiały metalowe do rzeźbienia obejmują stal hartowaną itp.
Jaki wpływ ma samo narzędzie skrawające na proces obróbki i jaki ma na niego wpływ?
Czynniki narzędzia tnącego, które wpływają na obróbkę grawerowania, obejmują materiał narzędzia, parametry geometryczne i technologię szlifowania.Materiałem narzędzia tnącego stosowanym w obróbce rzeźbiarskiej jest twardy materiał stopowy, który jest stopem proszkowym.Głównym wskaźnikiem wydajności, który określa wydajność materiału, jest średnia średnica proszku.Im mniejsza średnica, tym bardziej odporne na zużycie jest narzędzie i tym większa jest jego trwałość.Więcej wiedzy na temat programowania NC koncentruje się na oficjalnym koncie WeChat (nauczanie programowania NC), aby uzyskać samouczek.Ostrość narzędzia wpływa głównie na siłę skrawania.Im ostrzejsze narzędzie, tym mniejsza siła skrawania, płynniejsza obróbka i wyższa jakość powierzchni, ale mniejsza trwałość narzędzia.Dlatego przy obróbce różnych materiałów należy wybrać inną ostrość.Podczas obróbki miękkich i lepkich materiałów konieczne jest naostrzenie narzędzia tnącego.Gdy twardość obrabianego materiału jest duża, należy zmniejszyć ostrość, aby poprawić trwałość narzędzia tnącego.Nie może być jednak zbyt tępy, w przeciwnym razie siła skrawania będzie zbyt duża i wpłynie na obróbkę.Kluczowym czynnikiem podczas szlifowania narzędzi jest rozmiar oczek precyzyjnej ściernicy.Ściernica o dużych oczkach może wytwarzać drobniejsze krawędzie skrawające, skutecznie poprawiając trwałość narzędzia tnącego.Tarcze szlifierskie o dużym rozmiarze oczek mogą wytwarzać gładsze powierzchnie boczne, co może poprawić jakość powierzchni cięcia.
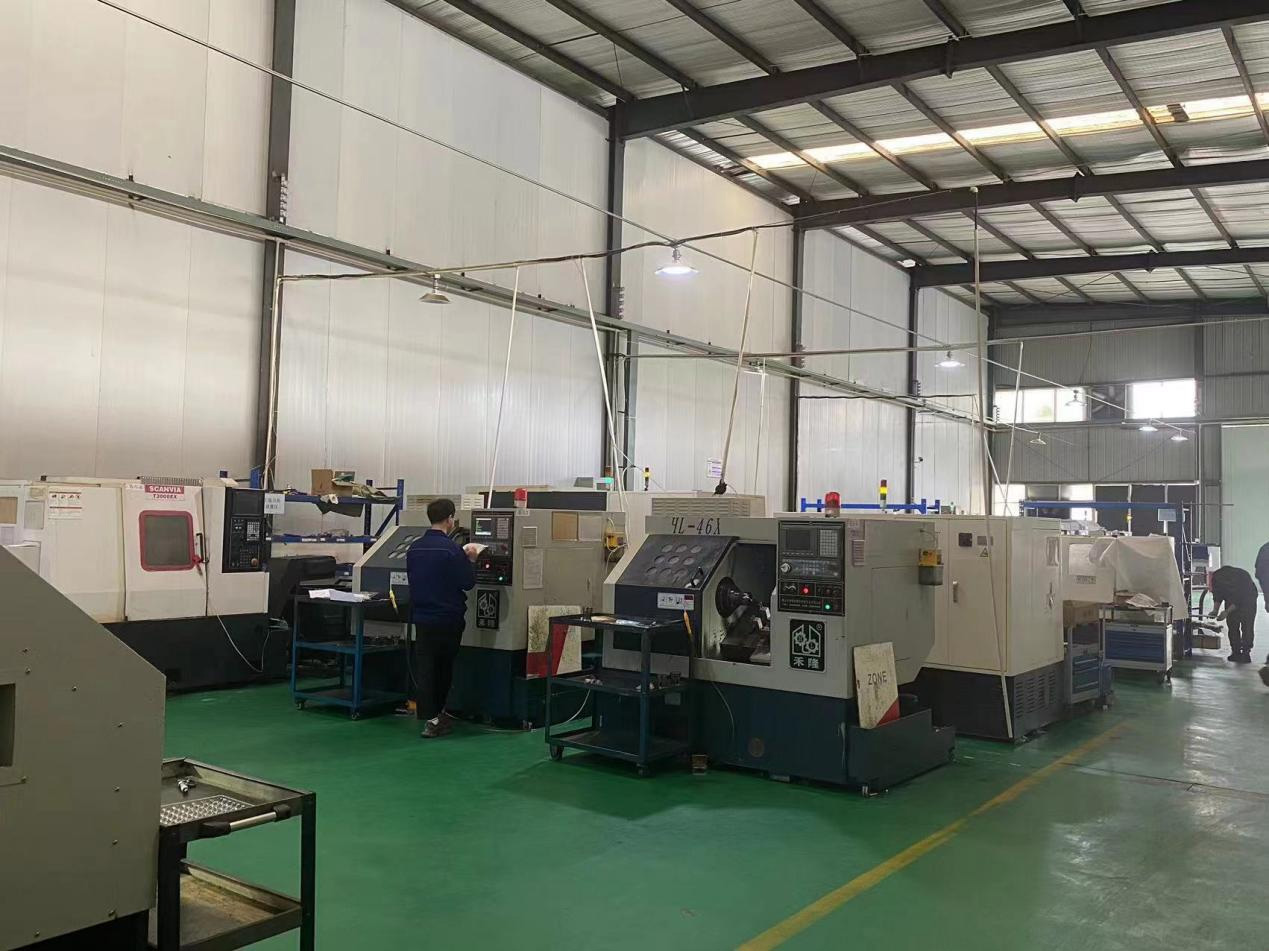
Jaki jest wzór na trwałość narzędzia?
Trwałość narzędzia odnosi się głównie do trwałości narzędzia podczas obróbki materiałów stalowych.Wzór empiryczny jest następujący: (T to trwałość narzędzia, CT to parametr trwałości, VC to prędkość linii skrawania, f to głębokość skrawania na obrót, a P to głębokość skrawania).Największy wpływ na trwałość narzędzia ma prędkość linii skrawania.Ponadto bicie promieniowe narzędzia, jakość szlifowania narzędzia, materiał i powłoka narzędzia oraz chłodziwo mogą również wpływać na trwałość narzędzia.
Jak chronić sprzęt maszyny rzeźbiarskiej podczas przetwarzania?
1) Chronić urządzenie do ustawiania narzędzi przed nadmierną erozją olejową.
2) Zwróć uwagę na kontrolę latających odłamków.Latające odłamki stanowią ogromne zagrożenie dla obrabiarki.Wlot do elektrycznej szafy sterowniczej może spowodować zwarcie, a wlot w szynę prowadzącą może skrócić żywotność śruby i szyny prowadzącej.Dlatego podczas obróbki należy odpowiednio uszczelnić główne części obrabiarki.
3) Podczas przenoszenia oświetlenia nie należy ciągnąć za trzonek lampy, gdyż może to łatwo spowodować uszkodzenie klosza.
4) Podczas procesu obróbki nie zbliżaj się do obszaru cięcia w celu obserwacji, aby uniknąć latających odłamków, które mogą uszkodzić oczy.Gdy silnik wrzeciona się obraca, zabrania się wykonywania jakichkolwiek operacji na stole warsztatowym.
5) Podczas otwierania i zamykania drzwi obrabiarki nie należy ich otwierać ani zamykać na siłę.Podczas obróbki precyzyjnej uderzenia i wibracje podczas otwierania drzwi mogą powodować ślady noża na obrabianej powierzchni.
6) Podaj prędkość wrzeciona, a następnie rozpocznij obróbkę, w przeciwnym razie ze względu na powolny start wrzeciona, żądana prędkość może nie zostać osiągnięta przed rozpoczęciem obróbki, co spowoduje uduszenie silnika.
7) Zabrania się umieszczania jakichkolwiek narzędzi i przedmiotów na belce poprzecznej obrabiarki.
8) Zabrania się umieszczania narzędzi magnetycznych, takich jak przyssawki magnetyczne i uchwyty czujników zegarowych na szafie sterowniczej, gdyż może to spowodować uszkodzenie wyświetlacza.

Jaka jest funkcja płynu chłodzącego?
Podczas obróbki metalu należy zwrócić uwagę na dodanie oleju chłodzącego.Zadaniem układu chłodzenia jest usuwanie ciepła powstałego podczas cięcia i latających zanieczyszczeń, zapewniając smarowanie podczas obróbki.Chłodziwo będzie przesuwać pas tnący, zmniejszając ciepło przekazywane do narzędzia tnącego i silnika, poprawiając ich żywotność.Usuń latające śmieci, aby uniknąć wtórnego cięcia.Smarowanie może zmniejszyć siłę skrawania i sprawić, że obróbka będzie bardziej stabilna.Podczas obróbki miedzi zastosowanie oleistej cieczy obróbkowej może poprawić jakość powierzchni.
Jakie są etapy zużycia narzędzia?
Zużycie narzędzi skrawających można podzielić na trzy etapy: zużycie początkowe, zużycie normalne i zużycie ostre.W początkowej fazie zużycia główną przyczyną zużycia narzędzia jest niska temperatura narzędzia, która nie osiąga optymalnej temperatury skrawania.W tym czasie zużycie narzędzia to głównie zużycie ścierne, które ma większy wpływ na narzędzie.Większa wiedza z zakresu programowania NC skupia się na oficjalnym koncie WeChat (nauczanie programowania sterowania cyfrowego), aby otrzymać samouczek, który łatwo może spowodować uszkodzenie narzędzia.Ten etap jest bardzo niebezpieczny i jeśli nie zostanie właściwie przeprowadzony, może bezpośrednio doprowadzić do złamania i awarii narzędzia.Kiedy narzędzie przechodzi początkowy okres zużycia i temperatura skrawania osiąga określoną wartość, głównym zużyciem jest zużycie dyfuzyjne, które powoduje głównie miejscowe łuszczenie się.Zatem zużycie jest stosunkowo niewielkie i powolne.Gdy zużycie osiągnie określony poziom, narzędzie staje się nieskuteczne i wchodzi w okres szybkiego zużycia.
Dlaczego i jak należy docierać narzędzia skrawające?
Wspomnieliśmy powyżej, że w początkowej fazie zużycia narzędzie jest podatne na pękanie.Aby uniknąć zjawiska pękania musimy wjechać w narzędzie.Stopniowo zwiększaj temperaturę skrawania narzędzia do rozsądnej temperatury.Po weryfikacji eksperymentalnej dokonano porównań stosując te same parametry przetwarzania.Można zauważyć, że po dotarciu żywotność narzędzia wzrosła ponad dwukrotnie.
Metoda docierania polega na zmniejszeniu prędkości posuwu o połowę przy zachowaniu rozsądnej prędkości wrzeciona, a czas obróbki wynosi około 5-10 minut.Podczas obróbki miękkich materiałów należy przyjąć małą wartość, a podczas obróbki twardych metali przyjąć dużą wartość.
Jak określić duże zużycie narzędzia?
Metodą określenia dużego zużycia narzędzia jest:
1) Posłuchaj przetwarzanego dźwięku i wykonaj ostry dźwięk;
2) Wsłuchując się w dźwięk wrzeciona zauważalne jest zjawisko zatrzymywania się wrzeciona;
3) Uczucie wzrostu wibracji podczas obróbki i wyraźne wibracje wrzeciona obrabiarki;
4) W zależności od efektu obróbki, obrobiony wzór dolnego ostrza może być dobry lub zły (jeśli tak jest na początku, oznacza to, że głębokość cięcia jest zbyt głęboka).
Kiedy należy zmienić nóż?
Powinniśmy wymienić narzędzie po osiągnięciu około 2/3 limitu trwałości narzędzia.Na przykład, jeśli narzędzie ulegnie poważnemu zużyciu w ciągu 60 minut, przy następnej obróbce należy rozpocząć wymianę narzędzia w ciągu 40 minut i wykształcić nawyk regularnej wymiany narzędzia.
Czy mocno zużyte narzędzia można dalej obrabiać?
W przypadku znacznego zużycia narzędzia siła skrawania może wzrosnąć trzykrotnie.Siła skrawania ma istotny wpływ na żywotność elektrody wrzecionowej, a zależność pomiędzy żywotnością silnika wrzeciona a siłą jest odwrotnie proporcjonalna do trzeciej potęgi.Na przykład, gdy siła skrawania wzrośnie trzykrotnie, obróbka przez 10 minut jest równoznaczna z używaniem wrzeciona przez 10 * 33=270 minut w normalnych warunkach.
Jak określić długość wysunięcia narzędzia podczas obróbki zgrubnej?
Im krótsza długość przedłużenia narzędzia, tym lepiej.Jednak w rzeczywistej obróbce, jeśli jest ono zbyt krótkie, długość narzędzia należy często regulować, co może znacznie wpłynąć na wydajność obróbki.Jak zatem należy kontrolować długość wysunięcia narzędzia skrawającego podczas rzeczywistej obróbki?Zasada jest następująca: φ Pręt narzędziowy o średnicy 3 można normalnie obrabiać po wydłużeniu o 5 mm.φ Listwę tnącą o średnicy 4 można normalnie obrabiać po wydłużeniu o 7 mm.φ Listwę tnącą o średnicy 6 można normalnie obrabiać po wydłużeniu o 10 mm.Podczas cięcia staraj się osiągnąć wartości poniżej tych wartości.Jeżeli długość narzędzia górnego jest większa od podanej powyżej wartości, należy starać się ją kontrolować do głębokości obróbki w momencie zużycia narzędzia.Jest to trochę trudne do zrozumienia i wymaga więcej szkolenia.
Jak sobie poradzić z nagłym pęknięciem narzędzia podczas obróbki?
1) Zatrzymaj obróbkę i wyświetl aktualny numer seryjny obróbki.
2) Sprawdź, czy w miejscu cięcia nie ma złamania ostrza i jeśli tak, usuń je.
3) Przeanalizuj przyczynę zepsutego narzędzia, co jest najważniejsze.Dlaczego narzędzie się zepsuło?Musimy dokonać analizy pod kątem różnych czynników wpływających na przetwarzanie wspomniane powyżej.Ale przyczyną zepsucia narzędzia jest nagły wzrost siły działającej na narzędzie.Albo jest to problem ze ścieżką, albo narzędzie się nadmiernie trzęsie, albo w materiale znajdują się twarde bloki, albo prędkość silnika wrzeciona jest nieprawidłowa.
4) Po analizie wymień narzędzie do obróbki.Jeżeli ścieżka nie została zmieniona, obróbkę należy przeprowadzić o jeden numer przed numerem pierwotnym.W tym momencie należy zwrócić uwagę na zmniejszenie prędkości posuwu.Dzieje się tak dlatego, że hartowanie w miejscu złamania narzędzia jest duże i konieczne jest także docieranie narzędzia.
Jak dostosować parametry obróbki, gdy obróbka zgrubna nie jest dobra?
Jeżeli przy rozsądnej prędkości osi głównej nie można zagwarantować trwałości narzędzia, podczas regulacji parametrów należy najpierw wyregulować głębokość skrawania, następnie prędkość posuwu, a następnie ponownie wyregulować prędkość posuwu bocznego.(Uwaga: Regulacja głębokości cięcia również ma swoje ograniczenia. Jeśli głębokość cięcia jest zbyt mała i warstw jest za dużo, teoretyczna wydajność cięcia może być wysoka. Jednakże na rzeczywistą wydajność obróbki wpływają inne czynniki, co skutkuje zbyt niską obróbką wydajność.W tym momencie konieczna jest wymiana narzędzia tnącego na mniejsze do obróbki, ale wydajność obróbki jest większa.Generalnie minimalna głębokość skrawania nie może być mniejsza niż 0,1mm.).
Czas publikacji: 13 kwietnia 2023 r