1. Before processing, each program shall strictly confirm whether the tool is consistent with the program.
2. When installing the tool, confirm whether the length of the tool and the selected tool head are suitable.
3. Do not open the door during machine operation to avoid flying knife or flying workpiece.
4. If a tool is found during machining, the operator must stop immediately, for example, press the "Emergency Stop" button or the "Reset Button" button or set the "Feed Speed" to zero.
5. In the same workpiece, the same area of the same workpiece must be maintained to ensure the accuracy of the operating rules of the CNC machining center when the tool is connected.
6. If excessive machining allowance is found during machining, "Single Segment" or "Pause" must be used to clear X, Y and Z values, and then milling manually, and then shaking back Zero "lets it run by itself.
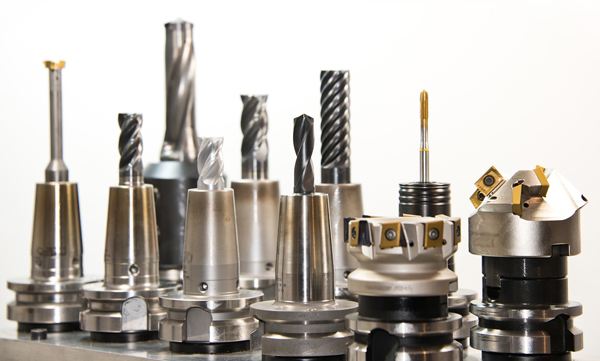
7. During operation, the operator shall not leave the machine or regularly check the running state of the machine. If it is necessary to leave midway, relevant personnel must be designated for inspection.
8. Before spraying the light knife, the aluminum slag in the machine tool shall be cleaned to prevent the aluminum slag from absorbing oil.
9. Try to blow with air during rough machining, and spray oil in the light knife program.
10. After the workpiece is unloaded from the machine, it shall be cleaned and deburred in time.
11. When off duty, the operator must hand over the work timely and accurately to ensure that the subsequent processing can be carried out normally.
12. Make sure that the tool magazine is in the original position and XYZ axis is stopped at the center position before turning off the machine, and then turn off the power supply and main power supply on the machine operation panel.
13. In case of thunderstorm, the power must be turned off immediately and the work must be stopped.
The characteristic of precision parts processing method is to control the amount of surface materials removed or added extremely finely. However, in order to obtain the precision of precision parts processing, we still rely on precision processing equipment and precise constraint system, and take ultra precision mask as the intermediary.
For example, for the plate making of VLSI, the photoresist (see photolithography) on the mask is exposed by the electron beam, so that the atoms of the photoresist are directly polymerized (or decomposed) under the impact of the electron, and then the polymerized or non polymerized parts are dissolved with the developer to form the mask. The positioning accuracy of mesa is required to be ± 0.01 for electron beam exposure plate making μ M ultra precision processing equipment.
Ultra precision part cutting
It mainly includes ultra precision turning, mirror grinding and grinding. Micro turning is carried out on an ultra precision lathe with finely polished single crystal diamond turning tools. The cutting thickness is only about 1 micron. It is commonly used for processing spherical, aspherical and plane mirrors of non-ferrous metal materials with high precision and appearance. Composition. For example, an aspherical mirror with a diameter of 800 mm for processing nuclear fusion devices has a maximum accuracy of 0.1 μ m. Appearance roughness is 0.05 μ m。
Special machining of ultra precision parts
The machining accuracy of ultra precision parts is nanometer level. Even if the atomic unit (atomic lattice spacing is 0.1-0.2nm) is taken as the target, it cannot adapt to the cutting method of ultra precision parts. It requires the use of special precision parts processing method, namely, applied chemistry.
Energy, electrochemical energy, thermal energy or electric energy can make the energy exceed the bonding energy between atoms, so as to eliminate the adhesion, bonding or lattice deformation between some external parts of the workpiece, and achieve the purpose of ultra precision machining These processes include mechanochemical polishing, ion sputtering and ion implantation, electron beam lithography, laser beam processing, metal evaporation and molecular beam epitaxy.
Post time: Jun-03-2019